Balancing Planet and Profit
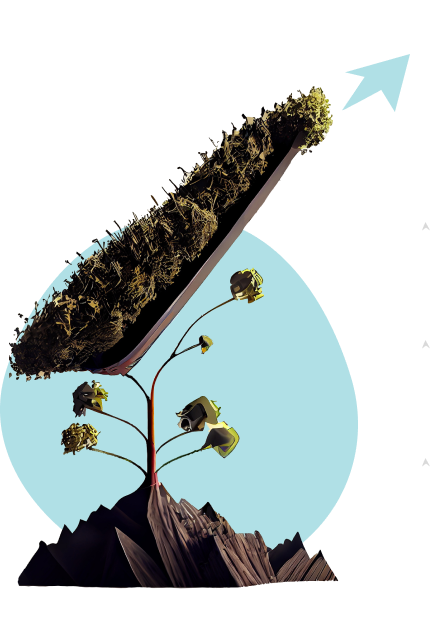
Collaborating with visionary enterprises, we architect tailored energy management strategies.
Our ambition: Empower our customers to collectively minimize emissions, harmonizing economic growth with ecological responsibility.
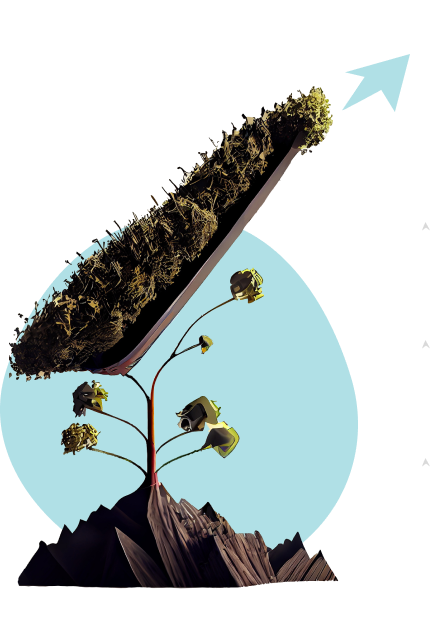
70+ Global Brands Trust CarbonMinus
Impact Figures
Electricity Savings
10,111,070
(kWh/Annually)
Cost Savings
905,192
(USD)
Emission Reduction
7,154
(tCO2e)
Your Strategic Path to Operational Savings
Charting a Route to Sustainable Energy Savings for a Chemical Manufacturer
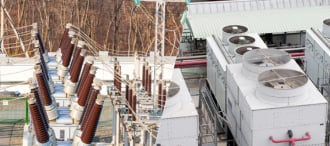
Impact in 1.5 years
1,024,424 kWh
Energy Saved
829.79 tCO2e
Emission Reduction
$ 112.95 K
Monetary Savings
For HT Furnace
Challenges
- Unmapped electrical network data.
- Unscrutinised transformer functioning and distribution losses.
Solution
- Implementation of real-time transformer health and power quality monitoring.
- Optimization of power quality and reduction of distribution losses.
Impact
Decreased electric distribution losses by
60%
Annual savings:
6,04,928 kWh
For Chillers
Challenges
- Lack of oversight on chiller and pump performance.
- Unchecked idle running due to knowledge gaps.
Solution
- Implementing performance tracking mechanisms for chillers and pumps.
- Activating alerts for idle run times and excessive consumption.
Impact
Idle run time decreased by
60%
Annual savings:
1,17,032 kWh
Elevating Efficiency Through
Focused Solutions for a
Aluminium Foundry
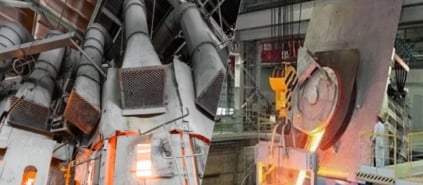
Impact in 2.75 years
648,000 kW
Energy Saved
524.88 tCO2e
Emission Reduction
$ 82.1 K
Monetary Savings
For HT Furnace
Challenges
- Lack of LPG dataand unidentified furnace heat losses.
- Non-conducted previous energy audits.
Solution
- Initiation of LPG monitoring and heat loss analysis.
- Application of insulation relining and thermo coating for heat loss mitigation.
Impact
Improved
LPG KPIs by
LPG KPIs by
10%
Annual LPG savings:
4800 kg
For 550kW Furnace
Challenges
- Excessive consumption and unmonitored KPIs in the induction melting furnace.
- Lack of familiarity with energy-saving protocols.
Solution
- Establishing energy monitoring and KPIs.
- Implementing optimal operating practices and personnel training.
Impact
Improved furnace’s KPIs by
15%
Annual savings:
2,16,000 kWh
Tailoring an Operational
Efficiency Strategy for
Foundry
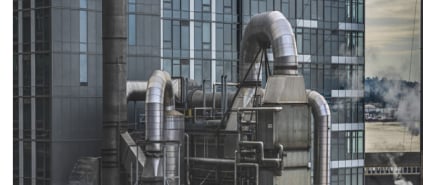
Impact in 2 years
3,26,640 kW
Energy Saved
264.5784 tCO2e
Emission Reduction
$ 35.3 K
Monetary Savings
For Air Compressor
Challenges
- Insufficient knowledge about compressor functionality and air leaks.
- Neglected energy inefficiencies and imprudent operations.
Solution
- Instituting monitoring for performance and air leaks.
- Sending alerts for energy wastage, loading issues, and incorporating air manager installation.
Impact
Reduced continuously running compressors by
34%
Annual
Savings:
Savings:
1,63,320 kWh
Elevating Efficiency Through
Focused Solutions for a
Machinery Manufacturer
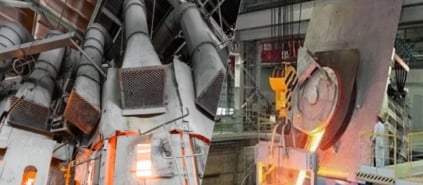
Impact in 2.75 years
648,000 kW
Energy Saved
524.88 tCO2e
Emission Reduction
₹ 68.32 Lakhs
Monetary Savings
For HT Furnace
Challenges
- Lack of LPG dataand unidentified furnace heat losses.
- Non-conducted previous energy audits.
Solution
- Initiation of LPG monitoring and heat loss analysis.
- Application of insulation relining and thermo coating for heat loss mitigation.
Impact
Improved
LPG KPIs by
LPG KPIs by
10%
Annual LPG savings:
4800 kg
For 550kW Furnace
Challenges
- Excessive consumption and unmonitored KPIs in the induction melting furnace.
- Lack of familiarity with energy-saving protocols.
Solution
- Establishing energy monitoring and KPIs.
- Implementing optimal operating practices and personnel training.
Impact
Improved furnace’s KPIs by
15%
Annual savings:
2,16,000 kWh
Charting a Route to Sustainable Energy Savings for a Chemical Manufacturer
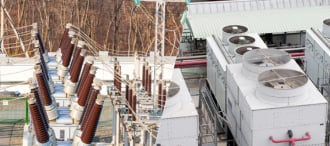
Impact in 1.5 years
1,024,424 kWh
Energy Saved
829.79 tCO2e
Emission Reduction
₹ 93.99 Lakhs
Monetary Savings
For HT Furnace
Challenges
- Unmapped electrical network data.
- Unscrutinised transformer functioning and distribution losses.
Solution
- Implementation of real-time transformer health and power quality monitoring.
- Optimization of power quality and reduction of distribution losses.
Impact
Decreased electric distribution losses by
60%
Annual savings:
6,04,928 kWh
For Chillers
Challenges
- Lack of oversight on chiller and pump performance.
- Unchecked idle running due to knowledge gaps.
Solution
- Implementing performance tracking mechanisms for chillers and pumps.
- Activating alerts for idle run times and excessive consumption.
Impact
Idle run time decreased by
60%
Annual savings:
1,17,032 kWh
Tailoring an Operational
Efficiency Strategy for
Castings Manufacturer
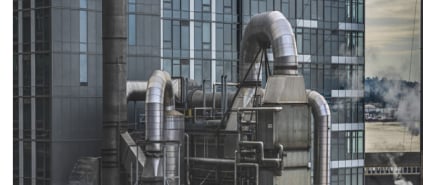
Impact in 2 years
3,26,640 kW
Energy Saved
264.5784 tCO2e
Emission Reduction
₹ 29.39 Lakhs
Monetary Savings
For Air Compressor
Challenges
- Insufficient knowledge about compressor functionality and air leaks.
- Neglected energy inefficiencies and imprudent operations.
Solution
- Instituting monitoring for performance and air leaks.
- Sending alerts for energy wastage, loading issues, and incorporating air manager installation.
Impact
Reduced continuously running compressors by
34%
Annual
Savings:
Savings:
1,63,320 kWh
HEAR FROM THE CHAMPIONS
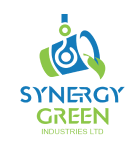
CarbonMinus's Energy Audit at Synergy Green honed our operations and aligned us with ISO50001 standards.

V. S. Reddy
Executive Director
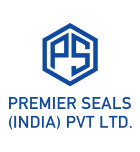
CarbonMinus's system at Premier Seals India pinpointed electrical inefficiencies, saving costs, and moving us closer to ISO50001.

Anuj Gupta
Director

CarbonMinus's EMAS at Vulkan Technologies not only boosted energy efficiency but has us on track for ISO50001.

Suhas Gavare
Head - Operations and Maintenance
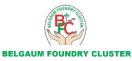
Implementing CarbonMinus's EMAS at Belgaum Foundry unlocked notable energy savings and is propelling us towards ISO50001.

Sadanand Hubarwadi
Secretary
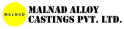
With CarbonMinus's EMAS, Malnad Alloy has seen a surge in energy efficiency and is advancing towards ISO50001.

Mahaveer Jain
Director of Operations & Quality Assurance
Ready to etch your mark in the green revolution?
Start your odyssey with CarbonMinus.