A blast furnace running at 1,500°C, churns out molten steel that will become the backbone of skyscrapers, bridges, and highways that we use every day.
An engineering marvel if you think about it. If you think deeper, it’s also an emissions disaster.
For centuries, heavy industry has powered civilizations, but it’s also pumped billions of tons of CO₂ into the atmosphere. Today, these industries—steel, cement, chemicals, and pulp & paper—account for over 30% of global carbon emissions.
Despite bold net-zero pledges, breakthrough innovations, and billions in investment, decarbonization in heavy industry remains slow, expensive, and frustratingly complex.
The challenge is that these industries were built around carbon and breaking that dependency isn’t easy.
Why It Matters Now
What heavy industries face now is a business problem. Companies that fail to adapt risk being left behind as global markets move toward cleaner, greener alternatives.
Regulatory & Investor Pressure:
- The EU’s Carbon Border Adjustment Mechanism (CBAM) is taxing carbon-heavy imports, meaning companies that don’t decarbonize could lose access to key markets.
- Investors are shifting billions toward low-carbon industrial technologies, rewarding companies with credible ESG roadmaps.
Economic Risk:
- The race for green steel, low-carbon cement, and sustainable chemicals is heating up. Companies that move too slowly will lose market share to cleaner competitors.
- Global carbon pricing is becoming an unavoidable cost for carbon-intensive industries.
Industries that don’t aggressively cut emissions will pay either in fines, lost revenue, or declining investor confidence.
The Hidden Gap: Why Heavy Industry Is Falling Short
Many companies believe they’re making progress because they’ve invested in carbon capture, switched to alternative fuels, or adopted energy-efficient technologies. But here’s the problem:
three key challenges in industrial decarbonization: lack of real-time energy optimization, reliance on outdated emissions reporting, and the use of estimated rather than real operational data.
Think about it: A steel mill running on hydrogen still wastes energy if it isn’t optimizing real-time energy flow. A cement factory with a carbon capture unit still bleeds efficiency if it doesn’t adjust energy consumption dynamically.
Without AI-powered insights and real-time tracking, companies aren’t truly decarbonizing—they’re just offsetting inefficiencies.
What This Blog Delivers
What’s Working: The AI, hydrogen, CCUS, and electrification strategies making a real impact in industrial decarbonization.
What’s Not Working: Why traditional models fail, where companies waste money, and the biggest blind spots in the industry.
What’s Next: The rise of AI-driven smart factories, decentralized industrial energy grids, and game-changing policy shifts.
What’s Working: Technologies & Strategies That Show Promise
For all the roadblocks slowing down industrial decarbonization, there are breakthrough solutions making real progress. From AI-powered energy optimization to green hydrogen and electrification, industries are seeing results.
But the catch is no single solution can solve the problem alone. Different industries require different approaches, and the most successful companies are the ones layering multiple strategies together—leveraging AI, alternative fuels, and next-gen infrastructure to decarbonize without sacrificing efficiency.
Let’s dive into the technologies that are already proving their worth.
AI-Driven Energy Optimization
Industrial production is an energy beast. Steel mills, cement kilns, and chemical plants all run at extreme temperatures, consuming vast amounts of electricity and fossil fuels.
But here’s the thing, much of that energy is wasted due to inefficiencies in heat processes, outdated maintenance schedules, and poor real-time visibility.
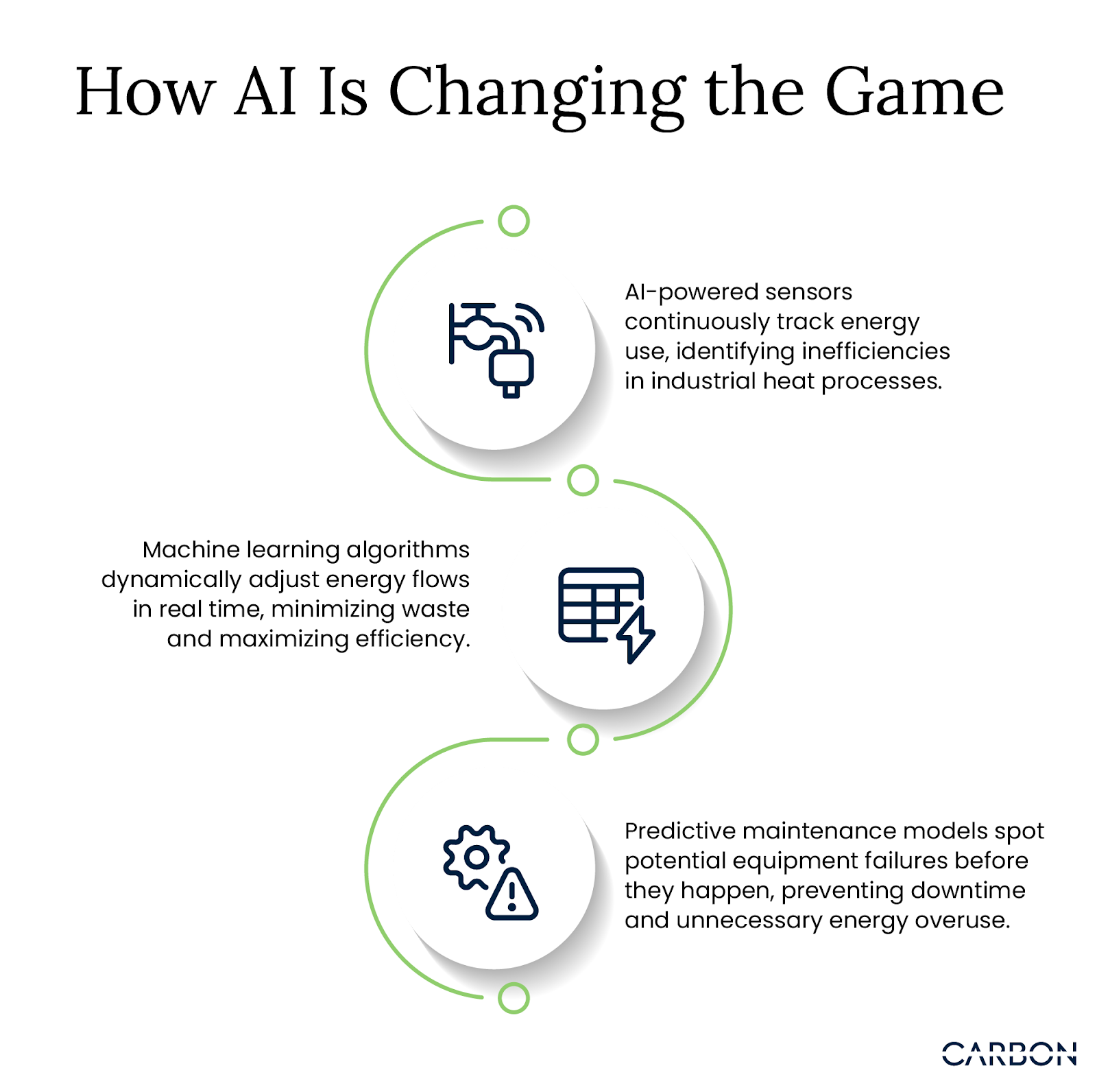
Real-World Impact: Companies leveraging AI-driven predictive maintenance are already cutting downtime and energy waste. AI’s ability to fine-tune industrial processes in real-time is turning reactive energy management into proactive energy optimization, saving millions in operational costs.
Hydrogen-Based Solutions
If there’s one thing that has the potential to revolutionize industrial decarbonization, it’s green hydrogen.
Why? Because it can replace coal, oil, and gas in some of the hardest-to-decarbonize industries, like steel production and refining.
Green Hydrogen in Steel
Traditional steelmaking relies on coal-fired blast furnaces, pumping huge amounts of CO₂ into the atmosphere. But companies like HYBRIT in Sweden are pioneering fossil-free steel, using green hydrogen instead of coal as the reducing agent in iron production.
The Challenges: Scaling Up
While the potential is enormous, hydrogen still faces major roadblocks:
1. Infrastructure isn’t ready—Most industrial plants aren’t equipped for hydrogen fuel use.
2. High production costs—Green hydrogen renewable energy is still expensive compared to fossil fuels.
3. Renewables dependency—Hydrogen production relies on surplus renewable energy, which isn’t always available at scale.
Despite these hurdles, hydrogen steelmaking is happening. And as production costs fall, this could be a defining technology for the future of low-carbon industry.
Carbon Capture, Utilization, and Storage (CCUS)
Even with hydrogen and electrification, heavy industries will still produce emissions for years to come.
That’s where Carbon Capture, Utilization, and Storage (CCUS) comes in, capturing CO₂ before it enters the atmosphere and either storing it underground or repurposing it into useful products.
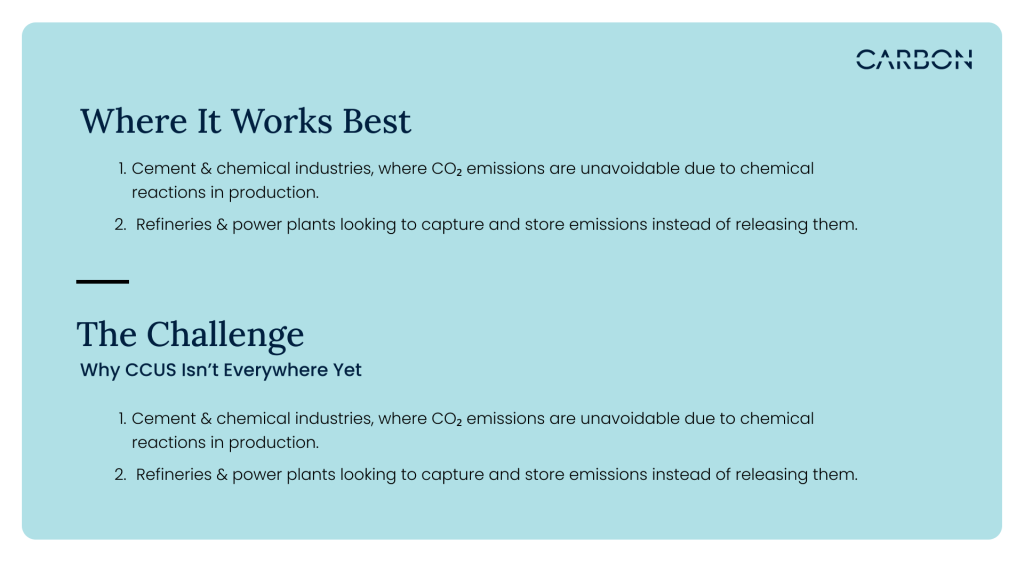
A Glimpse into the Future: Norway’s Longship Project
Norway’s Longship Project is leading the way in large-scale CCUS for cement plants, proving that capturing and storing carbon at an industrial scale is possible.
The big question now? Can we bring costs down enough for widespread adoption?
Electrification & Industrial Heat Pumps
For many industrial processes, the simplest way to cut emissions is to ditch fossil fuels entirely. Electrification is one of the most direct decarbonization strategies, especially when paired with renewable energy sources.
Why Electrification Is Critical
1. Switching from coal & gas heat sources to electric alternatives can reduce emissions by up to 40% in certain industries.
2. Industrial heat pumps allow factories to recover and reuse waste heat, cutting down overall energy demand.
The Challenges: The Grid Problem
1. Not all industrial processes can be electrified yet—some high-heat applications still rely on fossil fuels.
2. Mass electrification requires major grid upgrades—most power grids aren’t equipped to handle the massive demand shift.
But as hydrogen renewable energy capacity expands, electrification will become one of the most straightforward ways for industries to cut their carbon footprint.
Why These Technologies Matter
Each of these solutions—AI-driven energy optimization, green hydrogen technology, CCUS, and electrification—is playing a critical role in decarbonizing heavy industry.
But, where’s the friction? If these technologies are working, why isn’t the transition happening faster?
Next up: What’s NOT working and the biggest reasons industrial decarbonization is falling short.
What’s Not Working: Why Heavy Industry Is Falling Short
If technology is advancing, AI is optimizing, and companies are investing in low-carbon alternatives, why isn’t industrial decarbonization moving faster?
Because transitioning a system built on fossil fuels for centuries is about mindset, money, and operational reality.
Heavy industry is running into three major roadblocks: outdated sustainability models, the high cost of transformation, and deep-rooted resistance to change.
These issues are slowing progress and making decarbonization feel nearly impossible for some sectors.
Let’s break it down.
The Failure of Traditional Decarbonization Models
For years, industrial sustainability has been managed like an accounting exercise.
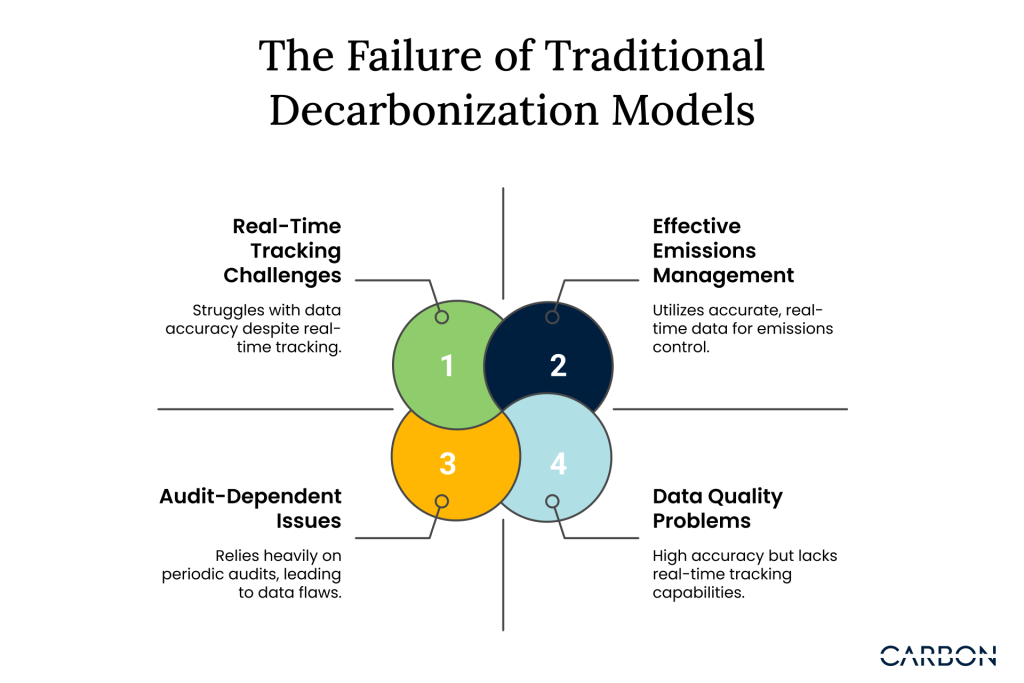
Companies conduct periodic emissions audits, make adjustments based on past data, and hope for the best. But in today’s high-stakes regulatory and investment climate, that approach doesn’t cut it anymore.
The Problem with Periodic Audits
Most industrial plants assess emissions data quarterly or even annually, meaning they’re always reacting too late to make meaningful reductions. By the time they analyze the data, the damage is already done.
Lack of Real-Time Emissions Tracking
Most companies don’t have live visibility into their emissions footprint. They’re still estimating, not measuring.
- Energy-intensive processes (like steelmaking or cement production) run on outdated efficiency assumptions, leading to huge but unnoticed energy waste.
- Production adjustments happen too slowly. Without real-time AI optimization, companies miss out on emission reduction opportunities that could be happening every second.
Bad Data = Bad Decisions
Suppose, a major steel producer discovers that it had overestimated its emissions reduction by 20%—not because it wasn’t taking action, but because its tracking methods were flawed.
Multiply this problem across the industry, and it’s clear why decarbonization efforts feel like they’re lagging behind expectations.
Industrial sustainability is failing because companies aren’t using real-time intelligence to drive decisions.
The High Cost of Transition
Even when companies want to decarbonize, many simply can’t afford it, or at least, that’s how it feels.
Green Tech Is Expensive—At Least for Now
1. Green steel production costs up to 50% more than traditional steel.
2. Hydrogen infrastructure requires billions in new investment—plants need retrofits, new pipelines, and massive renewable energy supplies.
3. Carbon capture and storage (CCUS) costs remain high, making adoption financially unviable for many companies.
Government Incentives Are Inconsistent
One of the biggest frustrations for industrial leaders is policy uncertainty.
- One year, a government offers massive subsidies for green hydrogen technology. The next year, funding shifts to other climate initiatives, leaving companies stuck with half-finished projects.
- Carbon pricing varies wildly by country, making long-term investment a high-risk gamble.
Policy Uncertainty Delays Green Hydrogen
Suppose, a U.S. chemical plant announced plans to transition to green hydrogen. But delayed the move indefinitely because subsidies were unstable, and the financial risks were too high.
When companies don’t know whether they’ll be able to recoup their investments, they hesitate and that hesitation slows everything down.
Cultural Resistance & Operational Complexity
Let’s be honest, decarbonization is also about people. And when people don’t like change, progress grinds to a halt.
Industrial Workforces Are Resistant to Change
1. Decarbonization is a massive operational shift.
2. Workers fear automation and AI could replace jobs.
3. Unions push back against process overhauls that could impact labor conditions.
Complex Operations Make Change Risky
1. Many industrial processes can’t afford downtime—even brief disruptions could cost millions.
2. Retrofitting old plants for new tech is logistically difficult—installing new energy systems in decades-old factories isn’t as simple as swapping out equipment.
Why These Challenges Matter
1. Bad sustainability models mean industries are making decisions with bad data.
2. High costs and unstable subsidies make long-term planning a nightmare.
3. Internal resistance slows down innovation, making change even harder.
So, what’s the way forward? How do we fix these problems and make industrial decarbonization happen faster?
Next up: The future of decarbonization—and the solutions that could finally make net-zero a reality.
What’s Next: The Future of Industrial Decarbonization
Imagine a factory that never wastes energy.
One where AI predicts when equipment will fail before it does, where machines self-optimize in real-time, and where waste materials don’t go to landfills but get repurposed into something valuable.
That’s not science fiction, it’s the future of heavy industry. And while today’s decarbonization efforts struggle with cost, complexity, and slow adoption, the next wave of innovation is poised to change everything.
From AI-powered smart factories to decentralized energy grids and industrial waste-sharing networks, the technologies emerging today are rethinking how industry works altogether.
Let’s look at what’s coming next.
The Rise of AI-Integrated Smart Factories
Industrial plants today are still operating with lagging data, outdated energy assumptions, and reactionary maintenance schedules.
The result? Massive inefficiencies and unnecessary emissions.
The Smart Factory Revolution
- AI-powered self-learning models dynamically optimize energy use in real time.
- Digital twins (virtual models of industrial systems) simulate process changes before implementation, minimizing risk.
- Predictive analytics prevents breakdowns before they happen, reducing downtime and wasted energy.
Next-Gen Carbon Capture And Utilization (CCU)
Right now, carbon capture is seen as an expensive last resort—a necessary evil for industries that can’t decarbonize fast enough. But what if captured CO₂ became a valuable resource instead of a problem?
Turning CO₂ into Profits
- Captured carbon can be converted into synthetic fuels, reducing the need for fossil fuels.
- CO₂ can be used in construction materials, industrial chemicals, and even consumer products.
- Companies like Carbon Clean are already proving that carbon capture can be a revenue driver.
Why This Matters
For industries that simply can’t eliminate all emissions (yet)—like cement and refining—this approach flips the script. Instead of paying for carbon storage, industries can turn emissions into something valuable, shifting from damage control to innovation.
Decentralized Energy Systems & Industrial Symbiosis
Right now, most industries rely on centralized power grids, which means they’re stuck with whatever energy mix the grid provides. But what if factories could generate, store, and manage their own energy on-site?
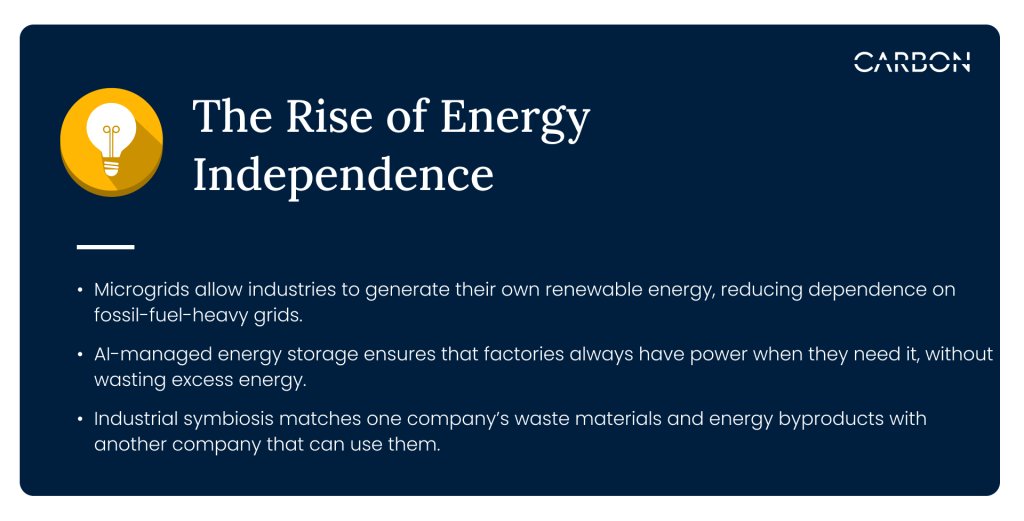
Real-World Use Case: A pulp & paper plant can reduce emissions using an AI-managed microgrid, optimizing when and how it draws power from different sources.
What this means: AI in heavy industry will create energy and distribute it intelligently.
Policy-Driven Transformation & Global Carbon Pricing
Because technology alone can’t drive change fast enough, so governments and financial markets are stepping in to force the issue.
Key Policy Drivers Shaping the Future
1. Carbon Border Adjustment Mechanisms (CBAMs)—The EU’s carbon tariffs mean high-emission companies will be taxed out of global markets.
2. Massive green energy funding—The U.S. Inflation Reduction Act ($370B in funding) is supercharging industrial decarbonization.
Why This Matters
Policies like CBAM mean that carbon-heavy industries lose their competitive edge entirely. Companies that act now will future-proof their operations, while those that don’t will find themselves locked out of key markets.
Why These Changes Matter
1. AI-driven smart factories will cut energy waste at the source.
2. Next-gen carbon capture will turn CO₂ from a liability into an asset.
3. Decentralized energy grids will give industries control over their own energy future.
4. Stronger regulations will force action—whether industries are ready or not.
So, where does this leave us? What will it take for industries to actually make this shift—at scale, and in time?
Next up: The final piece of the puzzle—why real-time data is the missing key to rapid decarbonization.
The Urgent Need for Real-Time Data in Decarbonization
For all the breakthroughs in industrial decarbonization—AI-driven optimization, green hydrogen technology, carbon capture, and decentralized energy—one thing remains painfully clear: most companies are still flying blind.
They’re relying on annual sustainability reports, outdated emissions tracking, and delayed policy responses to guide billion-dollar decisions.
And in a world where regulatory scrutiny, investor expectations, and market pressures are moving in real-time, operating with lagging data is no longer an option.
Decarbonization, in fact, is about intelligence. And intelligence requires real-time visibility.
Key Takeaways: The Critical Role of Real-Time Data
Traditional decarbonization models are outdated
- Industries are still using static emissions reports and periodic audits to track their carbon footprint.
- Without real-time insights, inefficiencies go unnoticed, and opportunities for reduction are missed.
AI and machine learning will drive real-time emissions tracking and reductions
- AI-powered sensors and predictive analytics can pinpoint inefficiencies instantly, allowing companies to make adjustments on the fly.
- Digital twins will help simulate the impact of process changes before they’re implemented, reducing risk and maximizing efficiency.
Financial & regulatory incentives must evolve for industries to transition faster
- Carbon pricing mechanisms and global policies like CBAM will penalize industries that don’t decarbonize.
- Consistent government incentives will determine how quickly industries scale solutions like hydrogen and CCUS.
The Industries That Adapt Now Will Win
The heavy industry sector is at a turning point and the decisions being made today will determine the leaders and laggards of the net-zero economy.
Industries that embrace AI-driven, real-time decarbonization now will:
1. Reduce costs by optimizing energy use before waste happens.
2. Stay competitive as regulatory requirements tighten.
3. Attract investors and customers looking for real sustainability commitments.
Industries that hesitate will find themselves struggling against rising operational costs, supply chain disruptions, and lost market share.
Real-time data is the missing key to unlocking true industrial decarbonization.