Key Takeaways
- ESG, compliance, and infrastructure risk now intersect.
- Digital Twins offer real-time visibility and control.
- Predictive analytics reduce downtime and emissions.
- Simulation enables safer, faster operational decisions.
- The right platform integrates seamlessly with legacy tech.
- ESG is no longer a cost center. It’s a performance driver.
There’s a storm brewing and it’s already on radar.
No, not a weather event. This one’s man-made. And it’s hitting the Oil & Gas sector from all sides.
On one front, ESG investors are pulling capital from operators who can’t prove sustainability performance. On another front, regulators are fining companies who can’t meet their sustainability targets.
Big numbers. And not just for obvious violations, sometimes just for missing data.
Meanwhile, inside the fence, your gear’s not getting any younger. Systems that were solid 15 years ago are starting to drift.
Efficiency drops. Unplanned shutdowns creep in. And yeah, emissions spike when things break.
That’s the storm. Three constant pressures, all hitting at once.
- ESG scrutiny
- Regulatory firepower
- Operational fragility
All converging. Fast.
You can’t wait it out. You can’t spreadsheet your way through it. And staying still? That’s the riskiest move of all.
The smartest refineries are already adapting by deploying Digital Twins: living, breathing virtual replicas of their operations. These tools do more than monitor as they simulate, predict, and optimize.
What started as a compliance play is now a performance engine.
In this post, we’ll break down the three major threats facing Oil & Gas and how Digital Twin technology turns them into a competitive edge.
Want to see the ROI for your facility? Run the numbers here. The results speak louder than theory.
Let’s get into it.
What are the risks you can’t ignore anymore?
You’re not just dealing with one issue. You’re fighting three battles at once. And they’re all connected.
Let’s break it down.
1. The investor mandate: Capital’s on the move
If you can’t show ESG progress such as real data, not just good intentions, then you’re at risk of losing access to capital. It’s already happening.
Institutional investors are shifting funds toward companies that can prove they’re decarbonizing, optimizing, modernizing.
This is modern day risk management. They’re protecting their own portfolios.
So, if your facility can’t show transparent ESG metrics, it looks like a black box. And black boxes don’t attract capital. They trigger exit plans.
2. The regulatory squeeze: Fines are getting brutal
You’ve seen the headlines. $64.5 million here. $30 million there. Not for spills but for compliance gaps.
Bad data. Missing reports. Weak audit trails.
And the rules aren’t getting simpler, they’re only stacking up.
- CSRD in Europe
- GEI in India
- SEC drama in the U.S.
Even if enforcement’s uneven, the direction is clear: they want real-time, verifiable reporting. Anything less is a liability.
So when people call compliance a “cost center,” they’re missing the point. Done right, it’s risk protection.
3. The operational grind: Aging systems are dragging you down
Most infrastructure in Oil & Gas wasn’t built for the kind of real-time transparency you need today.
Turbines drift off spec. Steam systems leak. Compressors overheat.
You don’t always notice it… until it becomes downtime.
Every unseen inefficiency is money bleeding out of your system. And when a critical asset fails, you’re not just losing uptime.
You’re risking safety, emissions spikes, and a compliance incident in one hit.
This is what happens when reactive ops become the norm.
What is a digital twin and why does it matter now?
Let’s strip the jargon.
A Digital Twin is a live, digital replica of your physical operations. Could be a pump. A turbine. An entire refinery.
It’s not a 3D model. It’s a real-time simulation, constantly updated with live data from the field.
It sees what your systems see. It thinks faster than your engineers can. And it doesn’t sleep.
Don’t think dashboards. It’s about intelligence baked directly into your operations.
Let’s break down the three layers that make it powerful.
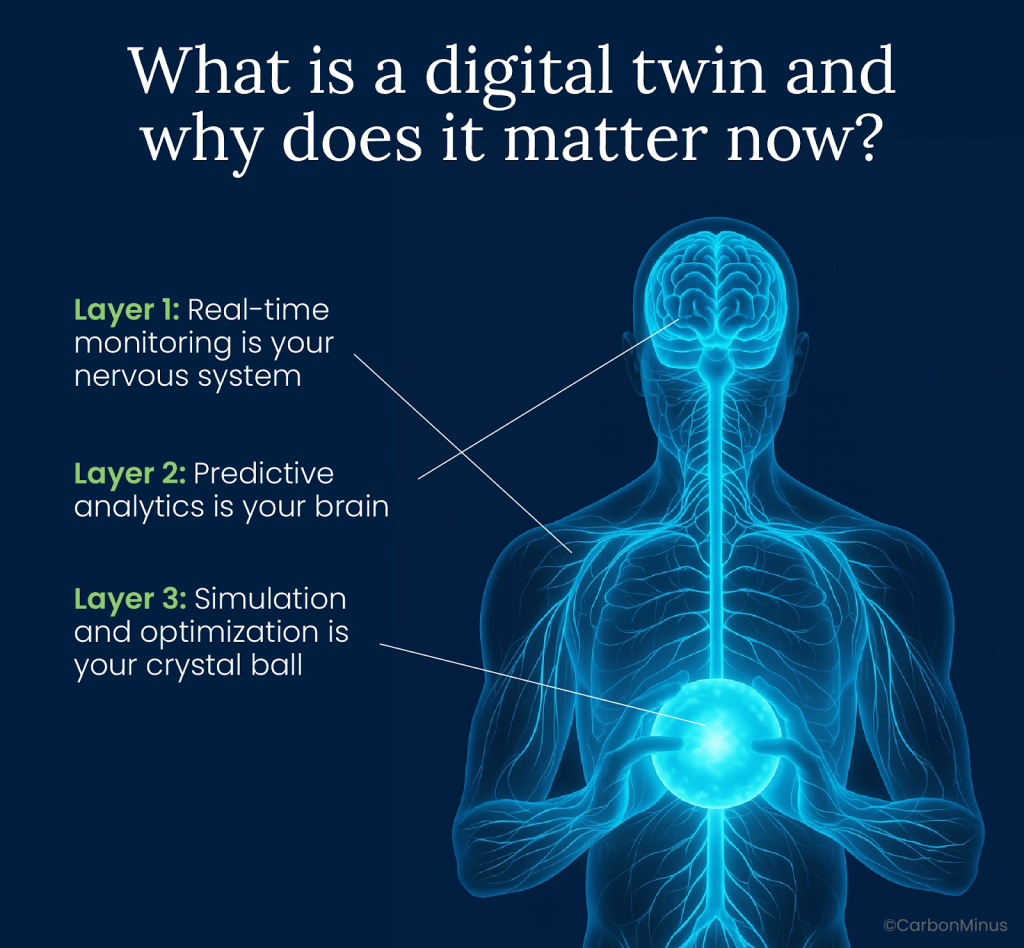
Layer 1: Real-time monitoring is your nervous system
Start with the basics. IoT sensors on your critical equipment like compressors, turbines, and chillers feed continuous performance data into the Twin.
You get 24/7 visibility. Not after the fact. Not at the end of the quarter.
Right now.
This kills the blind spots that come from legacy systems and paper-based reporting. When something’s off, you can act immediately.
Layer 2: Predictive analytics is your brain
Now that you’ve got the signals, it’s time to think ahead.
Machine learning models analyze that data in real time.
- They learn normal patterns
- Spot early warnings
- Predict when a failure is coming before it happens
No more “we’ll fix it when it breaks.” You’re into proactive maintenance, the kind that can cut downtime by 20% or more.
That’s fewer shutdowns, fewer emissions spikes, and lower operating costs.
All at once.
Layer 3: Simulation and optimization is your crystal ball
This is where things get fun.
You want to test new combustion settings? Swap a component? Add carbon capture?
You do it in the Twin first. Simulate the change. See the impact on emissions, efficiency, and cost before you touch the plant.
You’re no longer reacting to problems.
You’re stress-testing solutions and making better decisions with less risk.
What Should a Real Digital Twin Platform Deliver?
So you’re sold on the idea. But let’s be clear, not all “Digital Twin” platforms are built the same.
Some are just dashboards in disguise. Some need a full rip-and-replace to even get started.
And some are so narrow, they miss the point entirely.
If you’re serious about building resilience and getting a return, you need to demand three non-negotiables.
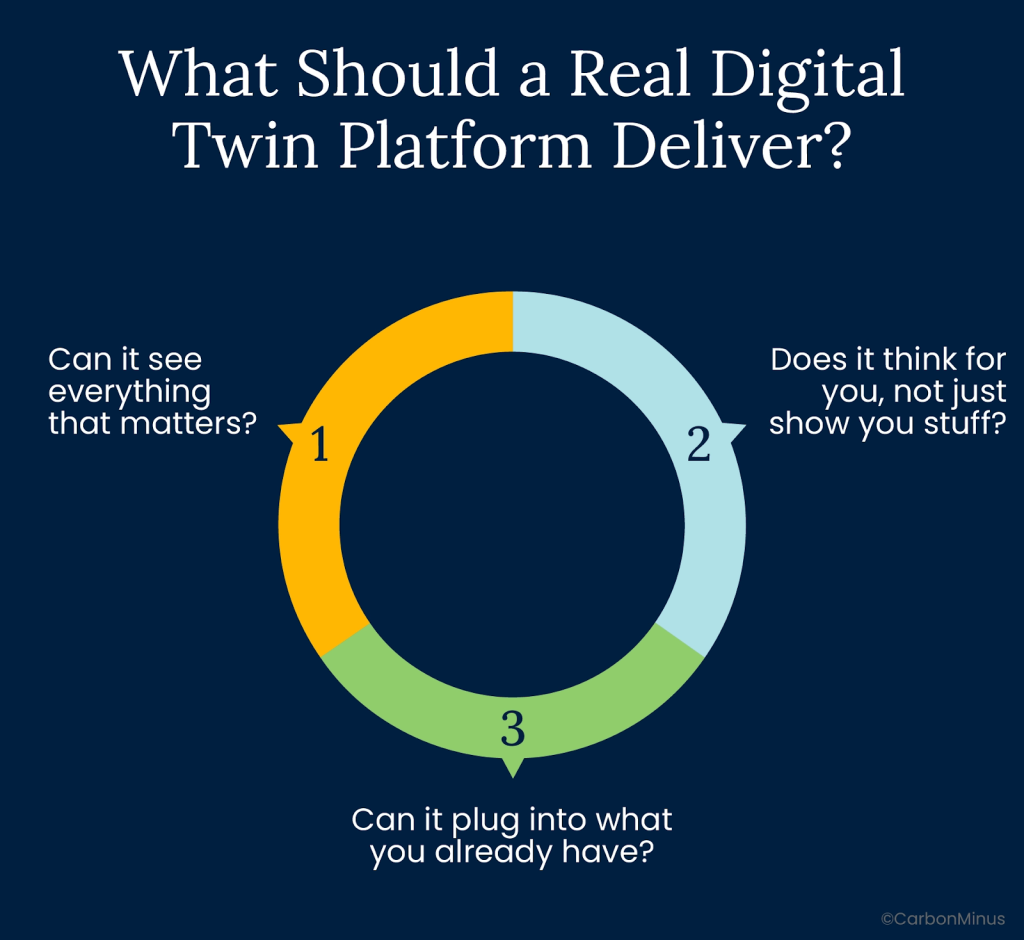
1. Can it see everything that matters?
If your platform can’t see the whole system, it can’t optimize it.
A real Digital Twin connects to all your critical systems including electrical grids, chillers, compressors, thermal networks, steam traps, everything.
It gives you live visibility across the board, not just isolated assets.
That means live SLDs (Single Line Diagrams), mass balance views, and energy flow models, which are the real engineering layer and not just KPIs.
It’s the difference between a weather app and a radar station.
2. Does it think for you, not just show you stuff?
You don’t need more data. You need guidance.
A proper platform doesn’t just dump analytics on your team. It flags issues early, tells you where the risk is, and offers prescriptive recommendations to fix it right there, in context.
Think: compressor X trending hot, adjust valve Y before it trips.
Not: Here’s a bunch of charts, good luck.
That’s what drives uptime. That’s what cuts energy waste. That’s what separates a system you check from one that actually makes you money.
3. Can it plug into what you already have?
If the platform needs you to rip out sensors, swap PLCs, or rewire your entire SCADA stack, it’s not practical.
A true solution should be hardware-agnostic. It connects to what’s already installed, talks to your ERP, and plays nice with your legacy tech.
Because real value doesn’t come from starting over, it comes from making your existing infrastructure smarter.
Fast rollout. Less downtime. Faster time-to-value.
From Surviving to Thriving
Let’s recap.
You’re not just managing emissions or filling out ESG reports. You’re managing investor expectations, regulatory risk, and operational volatility all at once.
And the old tools? They’re not enough anymore.
Digital Twins aren’t hype. They’re infrastructure for resilience, compliance, and profit.
They give you the real-time visibility, predictive power, and simulation insight to stay ahead of what’s coming.
Done right, they help you survive the storm and chart the course through it.
Ready to Turn ESG Risk Into ROI?
It starts with visibility. It scales with intelligence.
Use the CarbonMinus ROI calculator to see exactly how much profit you could unlock at your facility. Just input your annual energy bill and industry to get your result in seconds.
Want to see it applied to your operation? Book a strategy consultation. We’ll show you how to move from reactive sustainability measures to proactive control.
This is how you build the kind of refinery that can weather anything and come out stronger.
FAQs
What exactly is a Digital Twin and how is it different from a dashboard or SCADA system?
A dashboard shows you what’s happening. A SCADA system lets you control it. A Digital Twin does both, but smarter. It’s a real-time, dynamic model of your entire operation that can simulate, predict, and optimize performance. It doesn’t just tell you what went wrong. It tells you what’s about to go wrong and how to fix it before it costs you.
Our plant already has sensors and data systems. Why do we need a Digital Twin?
Sensors give you data. A Digital Twin turns that data into insight. It stitches all your systems together such as compressors, grids, and thermal networks to give you a live, complete picture. More importantly, it thinks ahead. You get early warnings, predictive analytics, and virtual testing capabilities. That’s not something you get from raw sensor data alone.
We’re dealing with aging infrastructure. Will this actually work in our environment?
Absolutely. In fact, that’s where Digital Twins deliver the most value. You don’t need to modernize everything first. A solid platform integrates with what you’ve got including PLCs, legacy SCADA, and old sensors to give you real-time visibility into systems that used to be blind spots. You don’t fix the problems by guessing. You fix them by knowing.
How fast can we see ROI from a system like this?
It depends on the scope, but in most cases you’ll see a measurable impact within months. Reduced downtime, better energy efficiency, and smarter maintenance cycles all add up fast. If you want a specific estimate, this ROI calculator is a good place to start. It’s built for exactly this kind of scenario.
Isn’t this just about ESG reporting?
Nope. That’s a bonus not the reason to do it. This is about operational intelligence. ESG compliance is a natural byproduct of running your assets better. When your data is accurate, real-time, and auditable, compliance becomes easy. But the real win is improved performance through lower costs, higher uptime, and fewer surprises.
Do we have to rip out or replace our existing systems to implement a Digital Twin?
No. And if someone tells you otherwise, they’re selling the wrong platform. A proper Digital Twin system is hardware-agnostic. It should integrate with what you’ve already invested in, no rip-and-replace required. It’s an overlay, not a do-over.
We’ve seen buzzwords come and go in this industry. Why is this different?
Fair question. The difference now? The tech finally caught up to the vision. We have the IoT coverage, the machine learning horsepower, and the integration tools to make it practical. And the pressure for ESG, regulation and operational risk isn’t going away. Digital Twins aren’t hype anymore. They’re survival tech.