Key Takeaways
- Over 50% of industrial energy is lost as heat. Most of it can be reclaimed.
- Heat reuse doesn’t require a district grid—internal and local applications work.
- Matching heat grade to demand requires real-time thermal mapping.
- The biggest barrier isn’t technology—it’s ownership and mindset.
- Circular heat strategies reduce energy costs, Scope 1 emissions, and ESG risk.
You see it every day—and miss it every time.
Steam billowing out of a vent stack. Chillers working overtime while jacket water gets dumped. Roof vents pulsing with warmth at dusk.
That’s energy you already paid for. Not waste. Not loss. Unclaimed value.
In most industrial plants, heat is treated like background noise. A byproduct. A maintenance burden. Something to manage, never something to monetize.
That mindset is outdated.
Industrial heat is the most reclaimable—and most neglected—form of circular value. Unlike raw material recovery or power purchase agreements, it doesn’t require new input or new contracts. It just requires a new lens.
Because the real opportunity isn’t generating more. It’s redirecting what you already have.
The Reality: Most Plants Are Bleeding Heat and Value
More than half of the energy that enters your plant leaves as heat. That’s not a metaphor.
That’s the International Energy Agency’s 2023 finding and it’s holding steady across sectors.
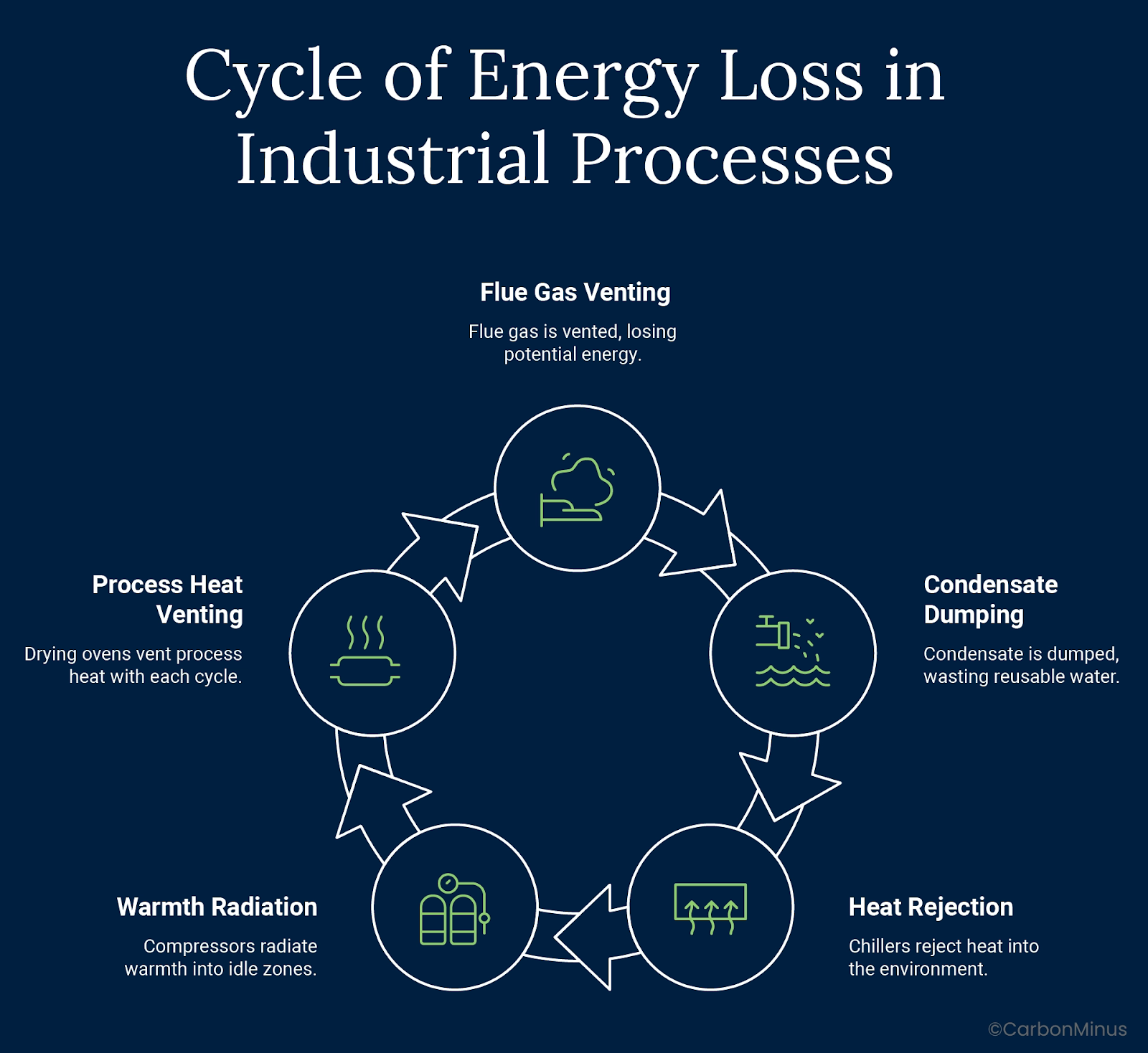
You lose it through:
- Flue gas vented before it can transfer value
- Condensate dumped instead of reused
- Chillers that reject heat into ambient air
- Compressors radiating warmth into idle zones
- Drying ovens venting process heat with every cycle
The problem isn’t the heat. It’s the invisibility.
Few plants measure thermal losses directly. Fewer still tag them to the systems or processes that created them. Without sensors or models, “heat loss” becomes a vague inevitability. It slips through the cracks of utility bills, maintenance logs, and sustainability reports.
Worse, there’s no internal marketplace. No one owns the heat. No one budgets for reuse. So it stays unclaimed.
So, it’s time to stop treating industrial heat as waste. Start treating it as inventory with latent demand, measurable flow, and strategic value.
Europe’s Advantage: Turning Heat Waste into Public Utility
Here’s what heat sharing looks like when done right:
In Denmark, industrial sites aren’t just powering factories—they’re heating neighborhoods. Waste heat from manufacturing lines flows into the national district heating grid, offsetting fossil demand and stabilizing energy costs for thousands.
In the Netherlands, a data center cluster near Middenmeer does more than process cloud traffic. It helps local greenhouses grow vegetables year-round by piping its excess heat straight to their walls.
In southern Germany, foundries facing winter energy spikes now supply their surplus process heat to nearby housing blocks—turning what used to be a liability into a seasonal asset.
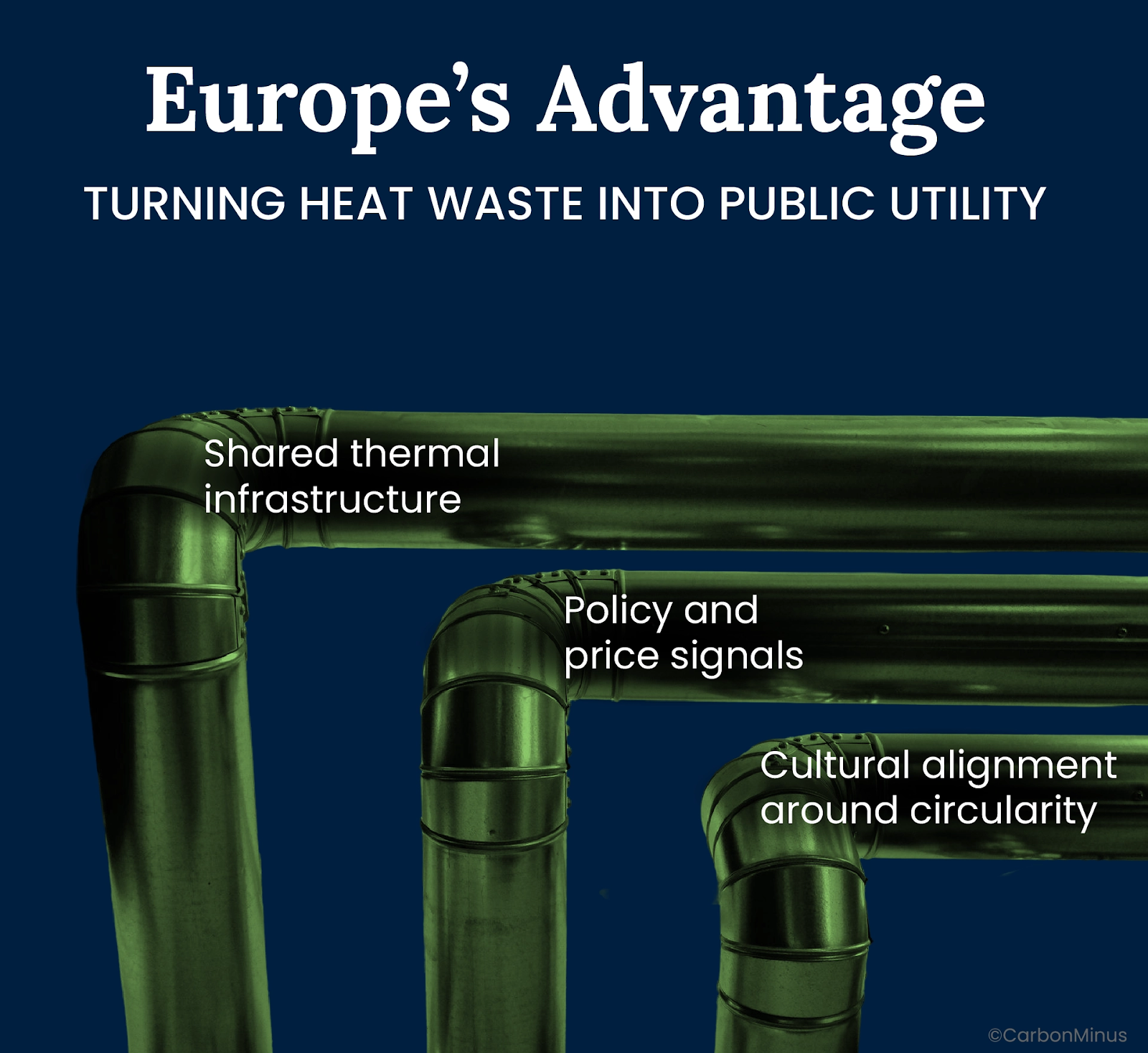
In Europe, industrial heat sharing works because three ingredients are in place:
Shared thermal infrastructure
In Denmark, some industrial parks are plumbed directly into district heating loops—so the heat leaving a food processing plant might be warming an apartment complex a few kilometers away. It works because the infrastructure was built with sharing in mind: pre-insulated pipes, metered exchange points, and centralized flow control.
Policy and price signals
But it’s not just the pipes. Policies back it up. Facilities get paid for recovered heat through feed-in tariffs, and avoided carbon is tracked through national GHG accounting. That turns heat reuse from a cost center into a revenue stream—or at least a compliance hedge.
Cultural alignment around circularity
And culturally, it’s expected. In parts of Germany and the Netherlands, if you’re dumping recoverable heat, you’re behind. Data centers supply greenhouses. Foundries offset school heating bills. It’s not seen as philanthropy. It’s efficiency with a local dividend.
Scalable Strategies for Any Facility: No District Grid Required
You don’t need a citywide heating grid to put waste heat to work. You need proximity, temperature data, and a plan.
Internal Reuse, First
Start where control is highest:
- Use dryer exhaust to preheat raw material in the same line.
- Capture jacket water heat to warm nearby utility rooms or floor slabs.
- Redirect chiller discharge into space conditioning systems—especially in colder months.
Local External Reuse
No need to sell heat across town. Start across the fence:
- Partner with an adjacent laundry, food processor, or greenhouse.
- Share thermal energy with nearby light industrial units—where hot water or intake air needs are steady and predictable.
Low-Bar Wins
Not every reuse path needs capex:
- Preheat combustion air with flue gas residuals.
- Use condenser heat to temper HVAC intake—especially in shoulder seasons.
Thermal Match Ladder
Temp Grade | Use Cases |
High (>200°C) | Process preheating, steam loops |
Medium (100–200°C) | Air drying, hot water, CIP systems |
Low (<100°C) | Space heating, intake tempering |
Why This Matters
Every reuse decision starts with matching supply to demand—by grade, duration, and timing. That takes data. Stack temperatures, flow patterns, and downtime logs. Then map them against viable sinks—inside or out.
What’s often missing isn’t hardware. It’s visibility.
From Mapping to Action: Building a Circular Heat Strategy
Capturing waste heat isn’t about plugging into a magical grid. It’s about knowing what you have, where it’s going, and how to put it to better use—step by step.
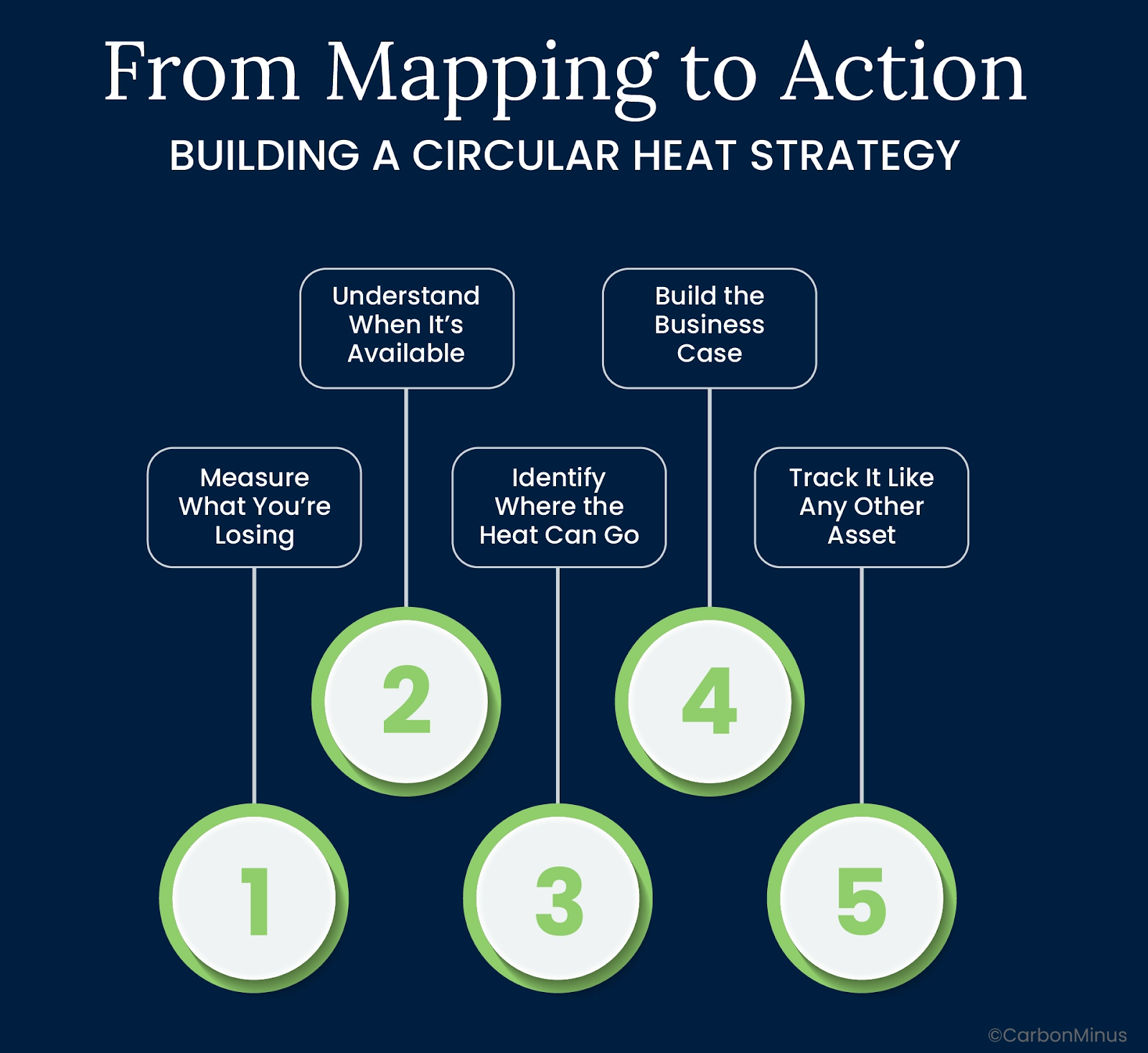
1. Measure What You’re Losing
Most plants don’t know how much heat they’re shedding or where. That’s the first gap.
Install:
- Stack temperature probes on flue gas outlets
- Jacket and shell thermocouples on heat exchangers, ovens, and furnaces
- Flow meters on condensate and cooling lines
- FLIR or thermal imaging to identify hotspots in real-time
It’s not about blanket monitoring. It’s about targeted instrumentation where thermal loss is high and usable.
2. Understand When It’s Available
Waste heat isn’t always steady or useful when you think it is.
Ask:
- Is this load batch or continuous?
- Does the temperature stay consistent or spike unpredictably?
- Is the heat available when the demand is active, or only in off-hours?
A perfect match on paper can fail in real time if the availability profile doesn’t sync with actual needs.
3. Identify Where the Heat Can Go
Once you know what you have and when, the question becomes: who or what can use it?
Inside your facility:
- Use dryer exhaust to preheat incoming material
- Route jacket water to floor heating in warehouses or offices
- Repurpose chiller waste heat for air handling units or make-up water
Outside your facility:
- Offer thermal energy to nearby laundries, food processors, greenhouses, or light manufacturing units
- Consider co-location strategies where waste heat can be designed into shared infrastructure
Critical insight: It’s not just about proximity. It’s about temperature grade, usage duration, and demand reliability. Without that alignment, the economics don’t hold.
4. Build the Business Case
Energy teams often lose support because they skip this step or oversimplify it.
Model:
- Avoided energy costs (fuel or electricity displaced)
- Retrofit and piping investments
- Maintenance overhead of reuse systems
- Potential revenue or ESG value from shared heat
Even modest reuse can yield strong ROI when you count carbon reductions, avoided capex elsewhere, or green certification benefits.
5. Track It Like Any Other Asset
Don’t let the recovered heat vanish into unmeasured “savings.”
Log:
- kWh recovered or fuel units offset
- CO₂e avoided (Scope 1 or 2 depending on source)
- Thermal reallocation rate: how much of available waste heat is actually reused
If you’re reporting under CSRD, BRSR, or targeting Scope 3 improvements—this is real data, not just narrative.
This Isn’t Just About Equipment
None of this works without integrated visibility. You need a platform that brings together thermal flow, asset telemetry, process timing, and operational load. If that sounds complex, it’s because plants weren’t designed with circular heat in mind. But that’s changing and the tools exist to make it practical.
The Barriers Are Real, But Beatable
If heat recovery is technically possible, why isn’t it everywhere?
Because the problem isn’t just pipes and pumps. It’s ownership. Visibility. Priorities.
1. No One Owns the Heat
Ask around: Who’s responsible for unused thermal energy? You’ll get silence.
- Maintenance focuses on uptime.
- Utilities manage cost.
- ESG tracks emissions.
Everyone touches it. No one claims it.
What helps: Assign clear accountability. Make thermal reuse part of someone’s KPIs—not everyone’s blind spot.
2. Heat Quality Doesn’t Match the Need
Not all heat is usable. Some is too low-grade. Some arrives at the wrong time. Some is just too far from where it’s needed.
- A 90°C stream won’t run your boiler.
- Batch heat can’t serve a 24/7 demand.
- A perfect match 100 meters away still needs capex.
What helps: Start small. Use what’s already close. Feed HVAC intake. Pre-warm process water. Build use cases before you build pipelines.
3. There’s No Line Item for Lost Heat
You can’t track what you don’t price.
- No one budgets for unrecovered kilocalories.
- Payback math ignores carbon.
- Financial models treat heat as a side note, not a resource.
What helps: Reframe the economics. Compare fuel spend with what’s recoverable. Factor in avoided emissions and compliance costs. Make waste visible—and costly.
4. It Doesn’t Feel Core, Until It’s Too Late
Heat recovery sounds nice. But it rarely feels urgent.
Until:
- A client asks for your Scope 1 roadmap.
- A buyer gives you points for circularity.
- A neighbor wants your waste heat—and you have no answer.
What helps: Treat heat like inventory. You paid for it. You’re producing it. You should know where it goes and how to use it better.
Bottom Line
The tech isn’t the issue. The mindset is.
Heat isn’t just a byproduct. It’s stranded value.
The plants that act now will end up saving more energy, while also building resilience, credibility, and a new kind of operational edge.
Your Facility Is Already a Power Plant: You Just Haven’t Capitalized On It
Every vented plume, every warm drain, every heat-soaked panel—that’s energy you already paid for. And then discarded.
Most plants treat heat as a loss to be managed. But it’s not loss. It’s value—stranded, overlooked, and increasingly reportable.
If a data center in Amsterdam can heat tomatoes, and a foundry in Berlin can warm homes, what’s your plant sitting on?
Circularity doesn’t need new tech. It needs a new lens.
Start with what you already generate. Measure it. Match it. Move it. Because your next competitive advantage isn’t a new input.
It’s the one you’ve been venting for years.
FAQs
Can I create value from waste heat without selling it?
Absolutely. Most plants see faster returns by using heat in-house, like preheating water, running low-temp drying, or reducing boiler loads. That cuts energy use and emissions without relying on external deals.
What derails most heat recovery projects early on?
Misalignment. Teams often focus on how much heat they can reclaim, not whether it matches a usable demand. The win comes from proximity, timing, and fit—not just volume.
We’re not a heavy industry. Does this still apply?
Yes. Food processors, cleanrooms, even data centers generate usable heat patterns. If you’re running repeat cycles or cooling large spaces, you’ve likely got recoverable energy sitting idle.
There’s no carbon credit for this, so how do I justify it?
Start with fuel savings. Then add the impact on equipment wear, system load, and ESG reporting strength. Even without tradable credits, circular heat lowers operating risk and shows up in your Scope 1 numbers.
What kind of team or role should own industrial heat strategy?
It needs a cross-functional champion—someone who can bridge operations, energy, and sustainability. Ideally, this person sits within Energy or ESG leadership but has direct access to plant data, utility spend, and maintenance logs. Circularity won’t work in a silo.