Key Takeaways
- Over 60% of industrial energy is lost as heat
- Most companies don’t treat waste heat as a resource
- Recovered heat = profit, efficiency, and lower emissions
- Adoption remains low due to outdated mindsets
- Real-time data and AI unlock full heat recovery potential
- Fragmented tech without a framework leads to waste
- WHOF enables continuous optimization and savings
- Regulatory and energy pressures make action urgent
- CarbonMinus unifies systems for measurable ROI
You’re burning money. Literally.
Every hour your furnaces run, your boilers churn, your reactors do their job — you’re losing heat. And not just a little.
Over 60% of industrial energy is wasted as heat. That’s billions of dollars, every year, escaping through chimneys, exhaust pipes, and cooling towers.
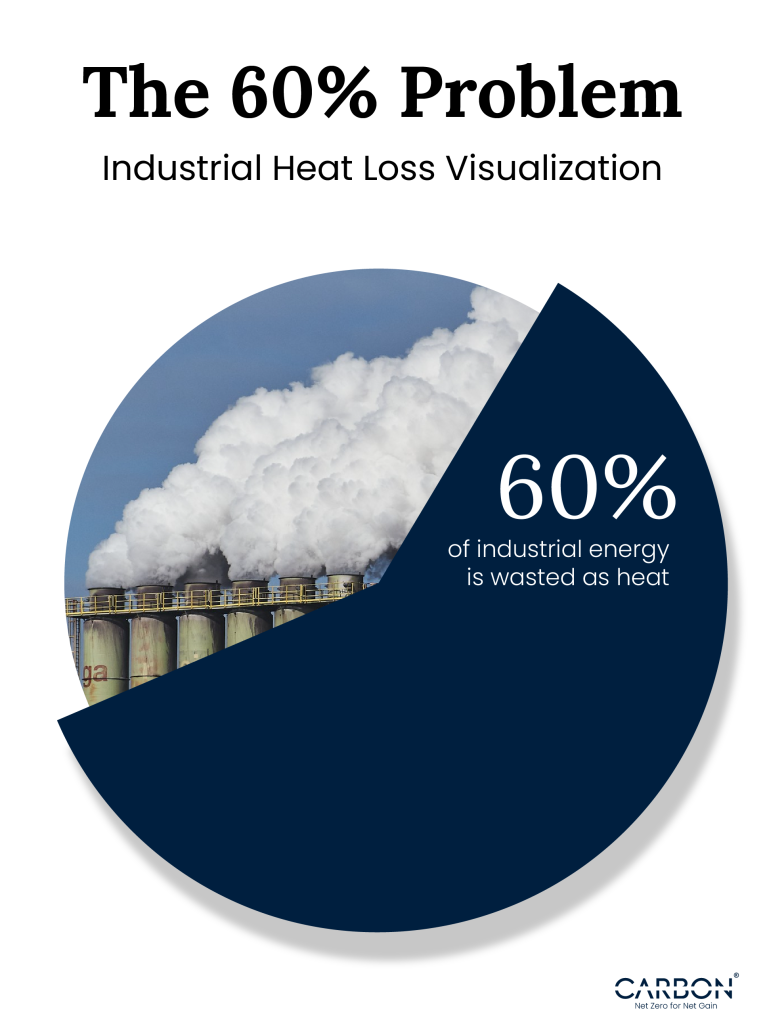
The steel industry alone? It loses nearly 50% of its energy input as heat.
Cement and glass manufacturing aren’t far behind. It’s like watching cash pour down the drain, day after day, while you’re busy chasing more obvious efficiency gains.
Everyone wants to cut emissions. Everyone wants to save energy. But when it comes to waste heat? It’s like trying to save a sinking ship by patching a leak while the hull’s ripped wide open.
Here’s the truth: The energy you’re ignoring isn’t just a lost resource. It’s a massive opportunity.
Capturing that waste heat could save you millions, boost your efficiency, and slash your emissions. But hardly anyone’s doing it.
Why? Because most companies don’t even see it as a resource. It’s an afterthought.
Something to be managed, not harvested.
In this article, we’ll show you exactly what you’re missing. We’ll break down the scale of the problem, why it’s ignored, and how advanced technologies can turn waste heat from a forgotten liability into a goldmine of savings.
What Industries Get Wrong About Heat Waste
Every industry wastes heat. But not every industry wastes it the same way.
The losses aren’t just big, they’re different. And unless you know what you’re looking for, you’ll never reclaim what you’re losing.
Steel Industry
Take the steel industry, for example. Most companies have heat recovery systems in place for basic processes like flue gas recycling.
But what about the heat lost through slag cooling or water quenching?
According to a study by the International Energy Agency (IEA), waste heat from slag cooling alone could recover up to 30% of the total energy input for some steel mills.
That’s millions of dollars left on the table.
Cement Manufacturing
Then there’s cement manufacturing. Everyone’s focused on kiln efficiency.
But what about the heat released during clinker cooling or the drying processes? Industry reports estimate that nearly 40% of all energy inputs in cement manufacturing are wasted through heat loss, primarily through outdated cooling systems and poorly insulated kilns.
Glass Production
In glass production as well high-temperature furnaces waste massive amounts of energy through radiation and exhaust gas. Studies suggest that more than 25% of all energy input is lost as heat and most of it is never recovered.
Chemicals and Petrochemicals Sectors
Similarly, the chemicals and petrochemicals sectors are notorious for energy losses during distillation, cracking, and other high-heat processes. According to the American Chemistry Council, waste heat recovery systems could improve energy efficiency by up to 20%. Yet, adoption remains limited.
Here’s the irony: The industries bleeding the most heat are often the ones most resistant to change.
Why Companies Keep Getting It Wrong
The real issue isn’t the heat you’re losing. It’s the way you think about it.
Most companies see heat loss as a cost of doing business — an inevitable by-product of high-temperature processes. It’s easier to accept the losses than to confront the massive investment required to fix them.
But the problem runs deeper than money. It’s psychological.
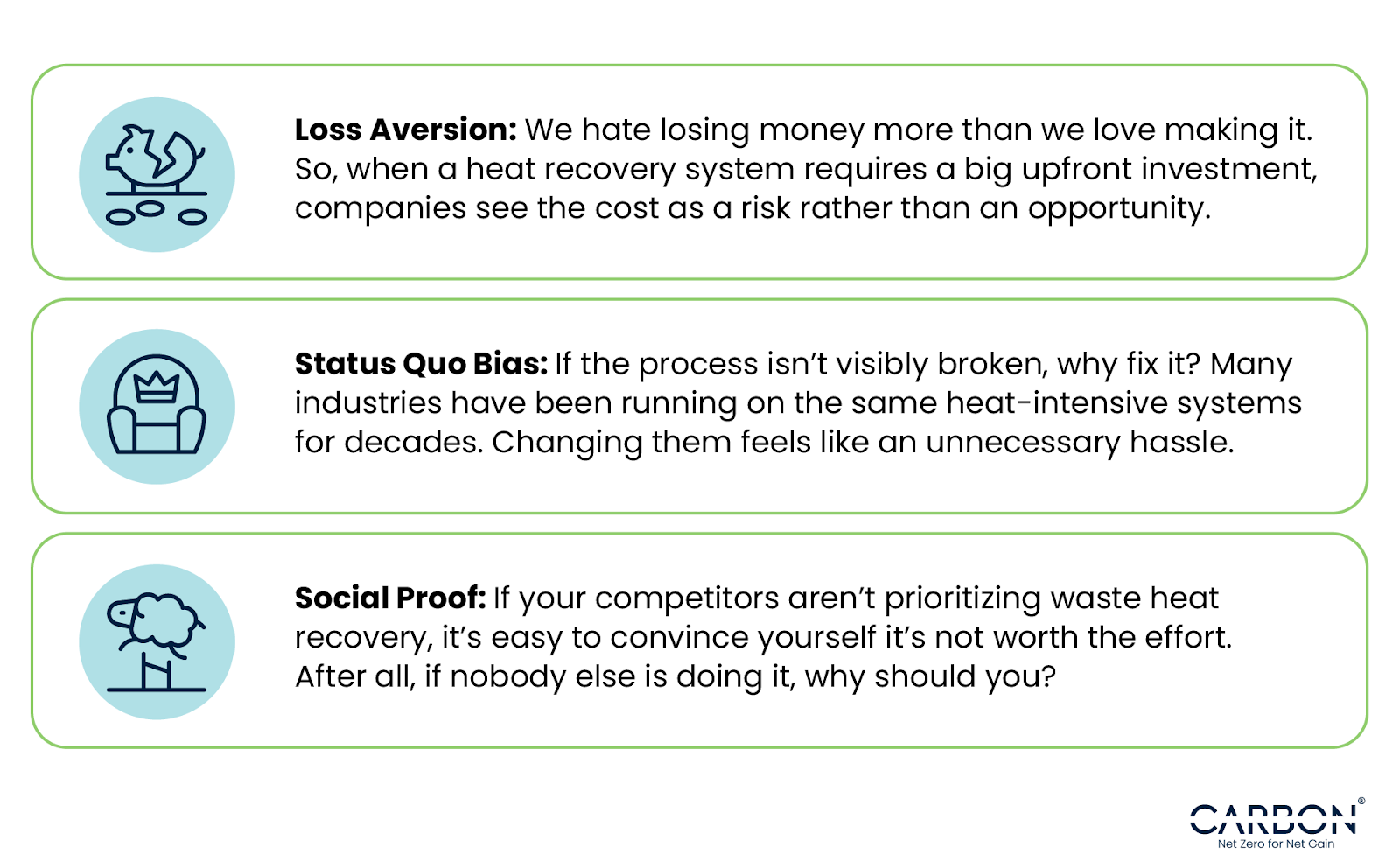
But here’s the kicker: Some companies are doing it. And they’re reaping the rewards.
The companies embracing waste heat recovery are cutting costs and securing their future against rising energy prices, tightening regulations, and consumer scrutiny.
They’re getting ahead while everyone else stays stuck in the past.
You don’t want to be the company playing catch-up when everyone else has already figured it out.
The heat you’re losing could be your biggest untapped resource. But only if you’re willing to see it that way.
Turning Lost Heat Into Profits
You’re surrounded by energy. You’re generating it every day through furnaces, kilns, boilers, reactors.
But most of it? It’s going up in smoke.
The good news? You can capture it.
And when you do, you’re not just cutting emissions, you’re turning a liability into profit.
The difference between companies that thrive and companies that coast? It’s not just what they do.
It’s what they refuse to waste.
Introducing the Waste Heat Optimization Framework (WHOF)
Most companies fail to reclaim waste heat because their approach is fragmented. They install a heat exchanger here, a thermal storage unit there, and hope for the best.
But without a framework to tie everything together, the results are always limited.
That’s why we present to you the Waste Heat Optimization Framework (WHOF)—a step-by-step approach designed to identify, capture, and optimize waste heat across your entire operation.
It’s not just about slapping on new technology. It’s about building a system that never stops improving.
Here’s how it works.
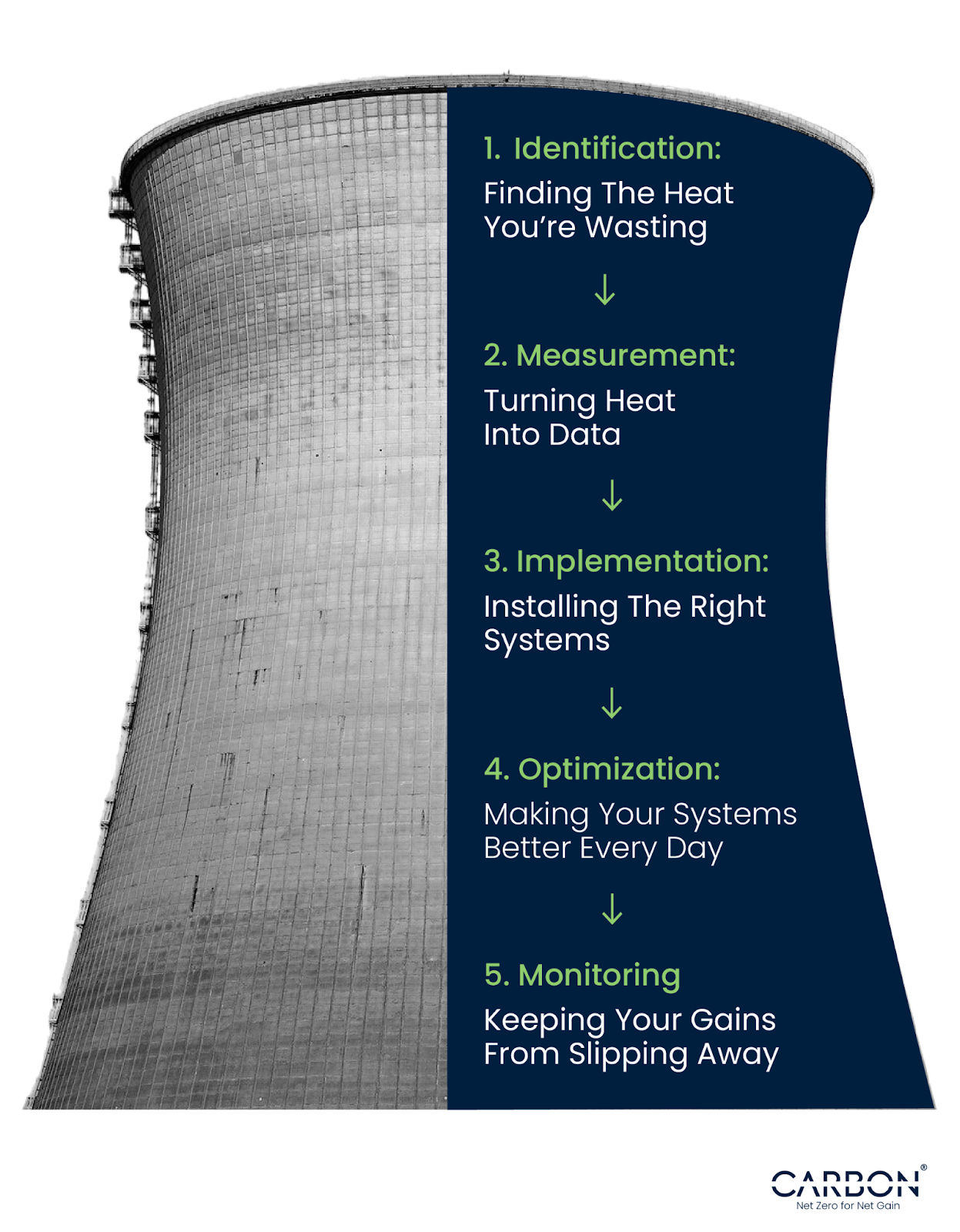
1. Identification: Finding The Heat You’re Wasting
Before you can recover lost heat, you have to find it. And that means pinpointing exactly where heat is being generated and lost.
In a steel mill, it might be the exhaust from blast furnaces or slag cooling. In cement manufacturing, it’s the kilns and clinker coolers.
Glass production? Your losses are likely tied to high-temperature furnaces and radiative heat.
The first step in WHOF is a comprehensive heat audit. Identify every single point of heat generation and loss because if you’re missing even one leak, you’re missing out on savings.
2. Measurement: Turning Heat Into Data
You can’t optimize what you can’t measure. That’s why real-time monitoring is critical.
Instead of waiting for quarterly reports or outdated spreadsheets, you need systems that track heat flow, temperature gradients, and energy use as they happen.
AI-driven tools can now provide continuous feedback, allowing you to pinpoint inefficiencies before they snowball into profit-draining disasters.
- Thermal Imaging Systems: Detect heat leaks and map out inefficiencies in real-time.
- Flow Meters: Track heat exchange rates and reveal where energy is being wasted.
- Smart Sensors: Provide continuous monitoring of temperature, pressure, and flow rates across your entire operation.
The more data you collect, the clearer your opportunities become.
3. Implementation: Installing The Right Systems
Now comes the part everyone jumps to before doing the groundwork. But you can’t just start using heat exchangers or thermal storage units and call it a day.
You’ve to choose the right technology for your specific process.
Here’s what works:
- Regenerative Heat Exchangers: Capture waste heat from exhaust streams and recycle it into the process. Ideal for high-temperature applications like glass and steel manufacturing.
- Heat Pumps: Transfer low-grade waste heat to a higher temperature where it can be reused. Perfect for chemical and petrochemical processes.
- Organic Rankine Cycle (ORC) Systems: Convert low-grade waste heat into electricity. Effective for industries with continuous, moderate-temperature heat sources.
- Thermal Energy Storage (TES): Store excess heat for later use. Useful for industries with fluctuating demand.
But here’s the mistake everyone makes: They treat these technologies as standalone fixes.
Without a framework to guide implementation, you end up with systems that work on paper but never deliver their full potential.
4. Optimization: Making Your Systems Better Every Day
Here’s where most companies drop the ball. They install the technology, then walk away.
But heat recovery systems aren’t set-and-forget. They need constant optimization.
And that’s where AI-driven analytics change the game, using continuous monitoring tools to keep your systems on track. But it doesn’t stop there.
The data you collect feeds into a feedback loop that automatically identifies inefficiencies and suggests improvements.
Every time you fix a problem, you’re creating a stronger baseline for future improvements. And the best part? It’s measurable.
With AI tools, you can track exactly how much energy you’re saving, how much carbon you’re cutting, and where your best opportunities for improvement lie.
5. Monitoring: Keeping Your Gains From Slipping Away
Once you’ve got your systems optimized, you need to make sure they stay that way. That’s why continuous monitoring and predictive maintenance.
You don’t want to wait until a boiler fails or a heat exchanger clogs before you take action.
By tracking performance metrics in real-time, you can prevent failures before they happen.
You’ll not only avoid breakdowns but also keep your systems operating at peak efficiency every single day.
Technological Solutions That Make It Possible
Different industries require different tools. Here’s how companies are making waste heat work for them:
- Steel: Regenerative heat exchangers installed in blast furnace exhaust systems.
- Cement: Organic Rankine Cycle systems recovering heat from kiln exhaust.
- Glass: High-efficiency thermal storage systems capturing radiative heat loss.
- Chemicals & Petrochemicals: Heat pumps and thermal energy storage systems improving efficiency during distillation and cracking.
Every industry has its own opportunities. But the companies that get ahead are the ones that use a framework, not just isolated technologies.
What CarbonMinus Brings To The Table
It’s important to have systems that work. But it’s more important to have systems that work together.
CarbonMinus’s predictive maintenance tools are built to integrate seamlessly with your existing processes. They provide real-time data, AI-driven insights, and continuous optimization.
The goal? To make sure every piece of your operation is running at peak efficiency—not just once, but always.
The heat you’ve been losing? It’s ready to be reclaimed. And every kilowatt you save is money back in your pocket.
To know more, you can reach us at https://carbonminus.com/contact-us/
What the Future Holds for Those Who Catch On
Some companies will get it. Most won’t.
And the difference? It’s the same thing separating market leaders from everyone else—who’s willing to adapt, and who’s stuck doing things the way they always have.
The opportunity is there for the taking. It’s expanding. And the companies that catch on now are the ones who’ll be ahead when everyone else wakes up to what’s been hiding in plain sight.
Applying WHOF to Specific Industries
Every industry generates heat. But not every industry generates the same kind of heat.
The key to making WHOF work? Tailoring it to your specific needs.
Steel Industry
You’re working with high temperatures. Blast furnaces, basic oxygen furnaces, electric arc furnaces—every step bleeds heat.
But here’s the twist: The heat you’re wasting is some of the most easily recoverable.
- Technology Fit: Regenerative heat exchangers, Organic Rankine Cycle systems, and high-efficiency recuperators.
- Future Outlook: As global steel production grows, waste heat recovery will become a competitive advantage rather than a regulatory afterthought. Expect stricter compliance requirements and higher energy costs.
Cement Industry
Kilns. Clinker coolers. Preheaters. Cement manufacturing is a furnace on overdrive.
And the hotter the process, the bigger the potential for heat recovery.
- Technology Fit: Organic Rankine Cycle systems, thermal energy storage, and kiln exhaust heat recovery systems.
- Future Outlook: Rising energy costs and emissions targets are forcing companies to rethink their heat management. Those who adapt will see cost savings and reputational boosts.
Glass Industry
Furnaces run at extreme temperatures, and every batch wastes energy through radiation, exhaust gases, and cooling.
- Technology Fit: High-efficiency thermal storage, recuperative burners, and waste heat boilers.
- Future Outlook: As the industry moves towards lower-carbon processes, waste heat recovery will play a critical role. Expect a push towards integrating renewable energy sources where possible.
Chemical & Petrochemical Industries
Your processes are energy-intensive and complex. From cracking and distillation to chemical reactions that produce heat as a by-product, there’s massive potential here.
- Technology Fit: Heat pumps, thermal energy storage systems, and regenerative heat exchangers.
- Future Outlook: Increasing scrutiny from regulatory bodies will make waste heat recovery not just a best practice, but a compliance necessity. Early adopters will have the advantage.
The Regulatory Push: Why Waste Heat Recovery Is About to Explode
Waste heat recovery helps save money and keeps you compliant.
The EU’s Corporate Sustainability Reporting Directive (CSRD), the U.S. SEC’s climate disclosure requirements, and India’s Perform, Achieve and Trade (PAT) scheme are all pointing in one direction: Operational efficiency is now mandatory, not an option.
But the problem with regulations? They focus on Scope 1 and Scope 2.
Scope 3 remains the wild west of carbon reporting. And that’s where waste heat recovery can make the biggest difference.
Companies that address waste heat as part of their Scope 3 strategy are cutting emissions drastically. They’re protecting themselves against future regulations that will almost certainly tighten around Scope 3 in the years to come.
Those who act now will be the ones setting the standard. Everyone else will be left scrambling to catch up.
Economic Drivers: Why This Is About More Than Compliance
Every time energy prices spike, waste heat recovery becomes more attractive. And with geopolitical instability and fluctuating fossil fuel markets, those spikes aren’t going away.
Here’s what companies that get ahead are already doing:
- Future-Proofing: Locking in savings by capturing heat that would otherwise be lost forever.
- Proving Sustainability: Showing customers, investors, and regulators that they’re doing more than just meeting the minimum standards.
- Reducing Costs: Cutting energy bills by reusing what they already generate.
And the companies that succeed? They have today’s prices. They’re planning for tomorrow’s disruptions.
Technological Innovations: How to Turn Waste Heat Into Profit in Manufacturing
Technology moves fast. And when it comes to waste heat recovery, innovation is happening everywhere.
- AI-Driven Predictive Maintenance: Using data to anticipate problems before they cause inefficiencies.
- Advanced Thermal Energy Storage: Storing excess heat for when it’s most needed, instead of letting it dissipate.
- Hybrid Systems: Combining renewable energy with waste heat recovery for near-zero carbon processes.
CarbonMinus is already at the forefront of this shift. Our systems help you find heat loss and optimize your operations continuously. And we do it in a way that integrates seamlessly with your existing processes.
What This Means For You
Waste heat recovery is no longer a checkbox on your sustainability report. It’s a profit center waiting to be unlocked.
Whether you’re working in steel, cement, glass, chemicals, or petrochemicals, the solution is already in front of you.
And the companies that make the first move? They’ll own the future.
The rest will be left chasing what’s already been taken.
Stop Losing What You Can Reclaim
You’ve seen the problem. You’ve seen the opportunity. Now it’s just a matter of who’s going to act first.
Most companies will keep running their operations the same way they always have, ignoring the billions in wasted heat that drifts away every year.
They’ll keep patching leaks and pretending that outdated systems are good enough.
But the ones who get it? They’re already turning lost heat into profit.
They’re cutting costs, lowering emissions, and proving to investors and regulators that they’re ahead of the curve.
And it’s not magic. It’s just a better way of doing things.
Every kilowatt you save is money back in your pocket. Every emission you eliminate is a step closer to compliance.
And the systems you optimize are a piece of your operation that’s working smarter, not harder.
You don’t have to rebuild your operation from scratch. You just have to start reclaiming what’s already yours.
The heat you’ve been losing? It’s your biggest untapped resource.
And the companies that figure that out now will own the future.
Know more at https://carbonminus.com/contact-us/
FAQs
Q: What’s the ROI timeline for waste heat recovery systems?
Most projects see payback within 2–5 years depending on scale, process heat intensity, and energy prices.
Q: What size or type of company benefits most from waste heat recovery?
Mid-to-large industrial plants with high heat processes (steel, cement, chemicals) see the largest gains, but even moderate heat losses add up quickly with the right framework.
Q: Is waste heat recovery applicable for low-temperature processes?
Yes—technologies like heat pumps and ORC systems can capture and reuse low-grade heat effectively, especially in chemical and food processing.
Q: How do I start if I’m unsure where my losses are?
Begin with a heat audit. CarbonMinus offers real-time thermal data tracking to map inefficiencies fast—no guesswork.
Q: Can waste heat recovery support Scope 3 reduction targets?
Absolutely. While waste heat recovery is often tied to Scope 1 or 2, outsourced heating and indirect emissions can be captured under Scope 3 strategy—especially if you extend tracking to suppliers.