Key Takeaways
- Cleanrooms often consume over 50% of facility energy due to strict control needs.
- Unvalidated HVAC changes can trigger microbial risk and deviation reports.
- Energy optimization must align with ISO 14644, EU GMP Annex 1, and CFR 211.
- Real-time monitoring of DP, RH, temperature, and ACH is essential.
- Zone-specific control, audit logs, and preemptive deviation alerts are non-negotiable.
- Systems should support validation-ready SOPs, not just energy savings targets.
You saved 12% on HVAC. Then you spent 10x on remediation after a deviation report.
That’s not a hypothetical, it’s a recurring theme in cleanroom operations.
In sterile manufacturing, the HVAC system is your primary control mechanism. It governs airflow, pressure, humidity, and temperature—all of which define your validated state.
Tweak them without context, and you’re not just chasing savings, you’re risking non-compliance.
The stakes are real
- One airflow dip can trigger microbial excursions.
- One pressure imbalance can collapse a cascade.
- One unverified setpoint change can jeopardize a full batch and its release timeline.
Cleanrooms don’t forgive approximation. And energy optimization, without precision, becomes a liability.
If your energy logic isn’t built for GMP conditions, it’s not optimization. It’s operational malpractice.
Cleanrooms: The Most Expensive Compliance System in the Building
Cleanrooms burn energy and convert it into compliance.
Didn’t get us? Let us explain what we mean.
Every air change, pressure hold, and decimal of RH control exists to meet the standards in ISO 14644, EU GMP Annex 1, and FDA CFR 211. These targets act as process guarantees, tied to batch integrity and product release.
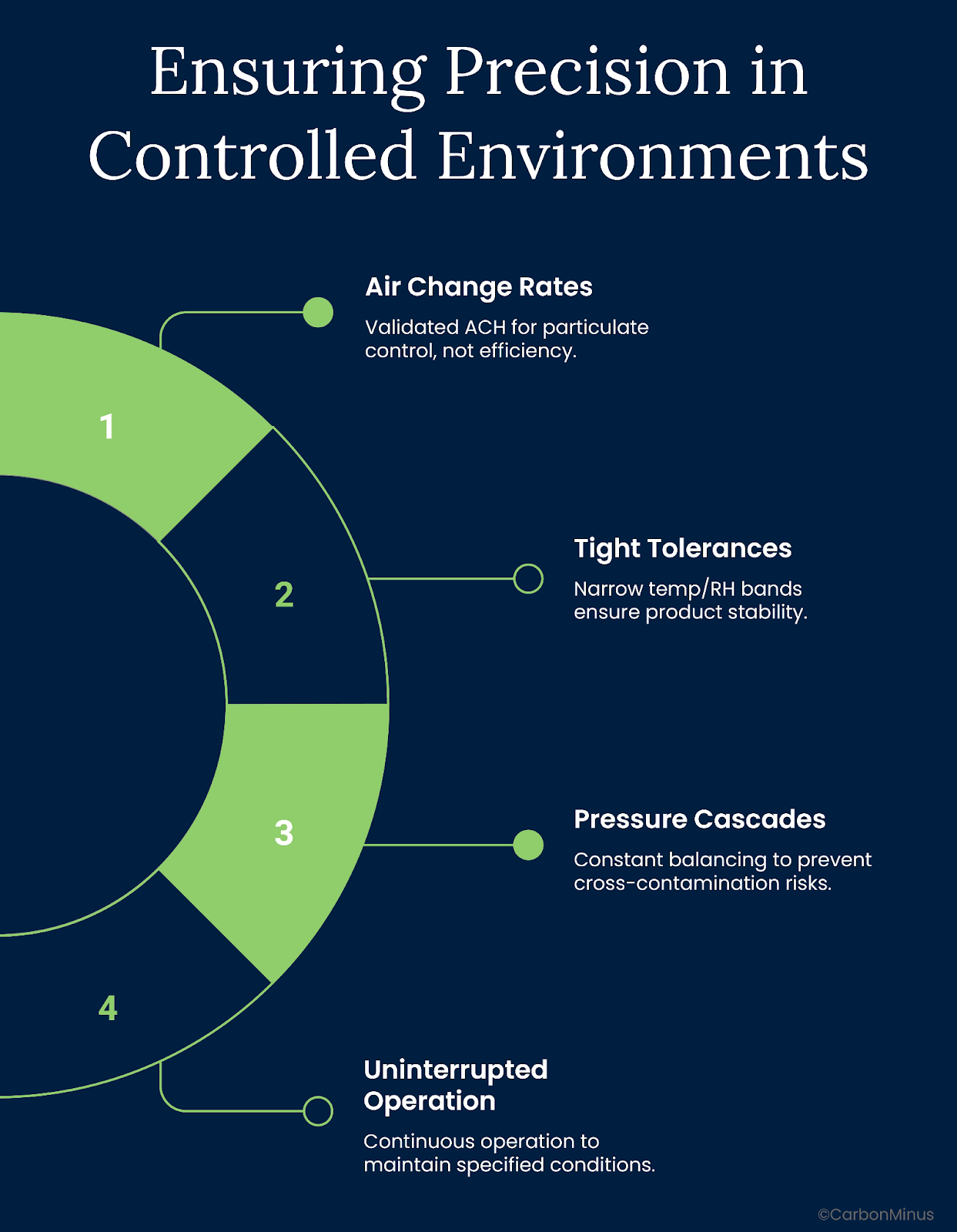
The result? Cleanrooms can consume up to 60% of a facility’s energy footprint even when they cover a fraction of the floorplan.
Why?
- Air Change Rates: 20–60 ACH, validated for particulate control, not efficiency.
- Tight Tolerances: Temp/RH bands are narrow by design to protect product stability.
- Pressure Cascades: Require constant balancing as any collapse risks cross-contamination.
- Uninterrupted Operation: No off switch. Even idle rooms must hold spec.
Here’s the gap: most energy strategies still treat cleanrooms like HVAC zones, not validated environments. They chase kWh savings with setpoint tweaks or filter swaps without realizing they’ve just violated their own qualification protocol.
Energy efficiency isn’t off-limits in cleanrooms. But unless it’s built on GMP-integrated feedback, it’s a liability waiting for a deviation report.
Where Optimization Goes Off the Rails
In cleanrooms, optimization without validation is just guesswork with consequences.
Too often, energy-saving tweaks happen in isolation—disconnected from the systems that actually hold GMP lines steady. And the results show up not in power bills, but in deviation logs.
Let’s break down where it goes wrong:
- Airflow cuts to “save fan energy” disrupt laminar flow. What follows? Turbulence, particle resuspension, and contamination risks.
- Seasonal temperature or humidity shifts—made to trim chiller load—can destabilize critical excipients or drift outside qualified bands.
- Filter replacements without real-time pressure checks can collapse the cascade hierarchy. The room stays “on,” but no longer protects the process.
The root cause isn’t malice or negligence. It’s separation. Facilities teams optimize for energy. QA teams monitor for excursions.
But the systems don’t talk, and the building behaves like a set of compartments, not a process-critical environment.
True optimization means feedback-driven control. Without zone-level data on pressure, RH, and particle count, you’re not fine-tuning. You’re gambling with compliance.
How to Optimize Without Compromise
Sure, energy efficiency in cleanrooms is about cutting more, but it’s also about cutting smart. You don’t need less control. You need better, validated control.
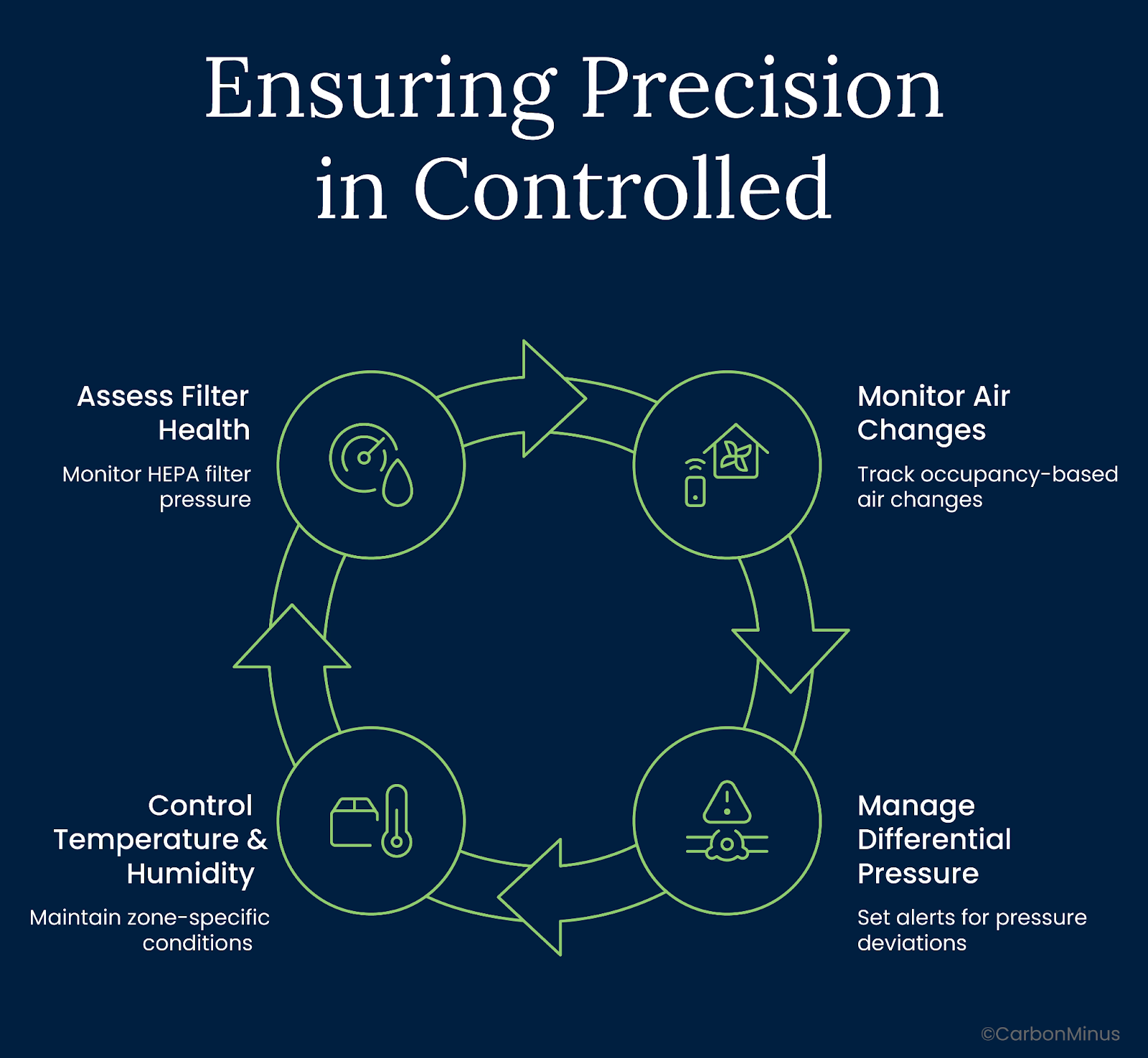
Here’s the framework high-performing GMP sites use:
Air Changes
Automate based on occupancy but never below validated thresholds.
If ACH drops below qualification levels, airflow loses directionality and risks particle buildup. Smart systems adjust dynamically but always stay within GMP bounds.
Real-time deviation logging ensures QA sees potential risks before they reach deviation status.
Differential Pressure
Set live alerts for ±10 Pa excursions.
Pressure integrity keeps clean zones clean. A cascade breach doesn’t always trigger a failure alarm—but it erodes control.
Trend degradation matters. Watch for slow loss of DP over time—it often signals filter saturation or fan imbalance.
Temperature & Humidity
Process zones need tighter bands than comfort zones.
±2°C and ±5% RH might meet spec, but in certain biologics or microelectronics, that’s still enough to impact yield or shelf life.
Use redundant sensors and per-zone audit logs. And make them QA-accessible, not just facility-facing.
Filter Health
Track HEPA differential pressure continuously.
DP drift tells you more than a calendar. Replace filters based on performance not arbitrary timelines.
And log every event for audit traceability.
These aren’t wishlist features. They’re essentials. And they require more than a BMS or building logbook.
Without an integrated, continuously monitored system, one that ties energy, environment, and validation together, you’re not optimizing. You’re flying blind.
The Integration Model: Compliance-Grade Energy Intelligence
A monthly HVAC report won’t save you from a deviation.
By the time a drift shows up in static data, the risk has already passed through your clean zone.
What today’s GMP environments demand is continuous, contextual visibility—a real-time ecosystem that connects air performance with process integrity.
Here’s what that looks like:
Live Zone Classification
Know your ISO class in real time, not just post-batch. Particle counts and airflow metrics should align visibly with the zone’s current classification, not its last validated state.
Unified Environment View
DP, RH, Temp, ACH—tracked together, not in silos. One dashboard. One source of truth. The moment one parameter drifts, the others must be interpreted in context. That’s how you catch cause, not just effect.
Real-Time Integration Isn’t Optional—It’s Protective
Most deviations don’t happen all at once. They build quietly across minor drifts in pressure, temperature, or airflow. But without linked systems, no one sees the pattern until it’s too late.
When environmental monitoring (EM) systems run separately from HVAC controls, risk gets buried in two dashboards. By the time QA spots it, you’re already explaining it.
Modern cleanroom infrastructure needs a shared lens. Not just raw data, but context:
When pressure starts to fall, is particle count stable?
If humidity drifts, is the HVAC system adjusting in time?
It’s not about alarms. It’s about alignment.
Suppose, at one biologics facility, early signs of pressure instability are caught by cross-trending airflow data with zone particle trends. It wasn’t a violation yet. But the facility responded fast.
The imbalance never escalated. The batch stayed safe. And QA stayed ahead of the audit.
No remediation. No production halt. Just quiet, compliant control by design.
What Can Be Optimized and What Must Be Validated
Not all energy tweaks are created equal. Some demand full revalidation. Others simply need better tracking. The real risk? Assuming you can’t touch anything—or worse, touching the wrong thing without oversight.
Here’s how smart facilities separate optimization from exposure:
Optimization Action | Revalidation Needed? | Risk Level | Practical Guidance |
Lower ACH in ISO 7 zone | ✅ Yes | High | Only cut air changes if you’ve got hard data—live EM trends, validated particle counts, and airflow direction tests. If laminar flow breaks, compliance goes with it. |
Reduce RH for energy savings | ✅ Yes | Medium | Before dialing humidity down, talk to QA. Changes in RH can shift excipient behavior or alter microbial resistance—not something you want to discover post-batch. |
Adjust temp ±1°C in core zone | 🔶 Maybe | Medium | Requires correlation with microbial trends and QA input. Not just an HVAC tweak. |
Preemptive HEPA filter swap | ❌ No | Low | Safe if pressure differentials remain intact before and after the change. |
Why it matters:
Compliance isn’t about saying no to efficiency, it’s about knowing where the line is, and proving you didn’t cross it.
This is where cleanrooms either build trust with QA or get buried in deviation reports.
If It’s Not Validation-Ready, It’s Not Ready
In cleanroom operations, energy efficiency isn’t a cost play. It’s a control strategy.
Every airflow tweak, every setpoint shift, every optimization must hold up to the same scrutiny as your product QA.
Because in a validated environment, failure isn’t just technical, it’s regulatory. And it’s expensive.
So here’s the rule: If it can’t be verified, logged, and defended in an audit, it has no place in your energy plan.
Efficiency doesn’t replace compliance. It reinforces it.
FAQs
How do I know if my current BMS setup is enough?
Start by asking this: Can your QA team catch drift before a deviation report lands? If you’re still piecing together logs from different systems or working off monthly summaries, you’re not getting the full picture. Most BMS platforms weren’t built for real-time GMP decisions—they track airflow, not audit trails.
What do early warning signs of risky energy changes actually look like?
You won’t always get alarms. What you will see: particle counts creeping upward, recurring borderline readings on differential pressure, and floor teams flagging comfort issues that don’t go away with a filter swap. Those are your tells—proof that “efficiency” might be chipping away at control.
How do I get leadership to back validation-first energy planning?
Show them where the risk lives. A minor energy tweak might save a few lakhs a year. A single deviation report can cost ten times that in wasted product and investigation overhead. The pitch isn’t about saying no to savings—it’s about proving where the line is between smart and shortsighted.
Can energy systems handle complex zoning in multiproduct sites?
If they’re built right, yes. Each cleanroom zone has different tolerances based on classification, product, and process step. A control system worth its salt can respond to each zone independently—not flatten them under the same logic. That’s how you scale without slipping.
Which standards matter most when upgrading cleanroom monitoring?
Start with the ones you can’t afford to fail: ISO 14644 for cleanroom classes, EU GMP Annex 1 for sterile manufacturing, and FDA 21 CFR Part 11 for audit trails. If ESG is in play, loop in ISO 50001 (energy) and ISO 14064 (GHG). They’re not just about compliance—they’re about proof.